
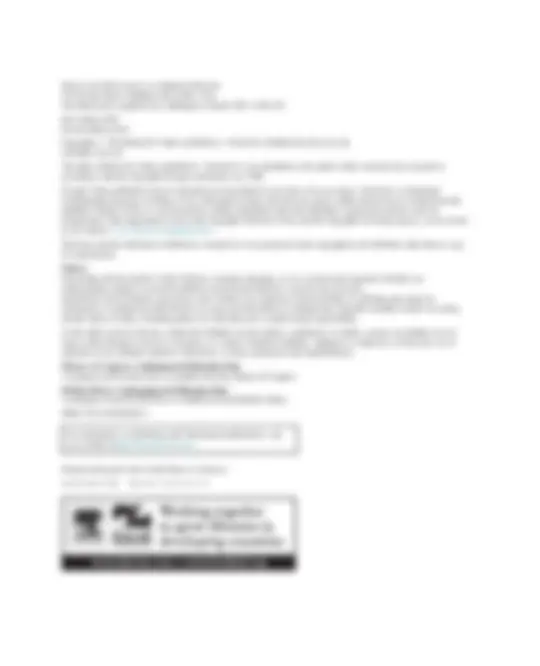
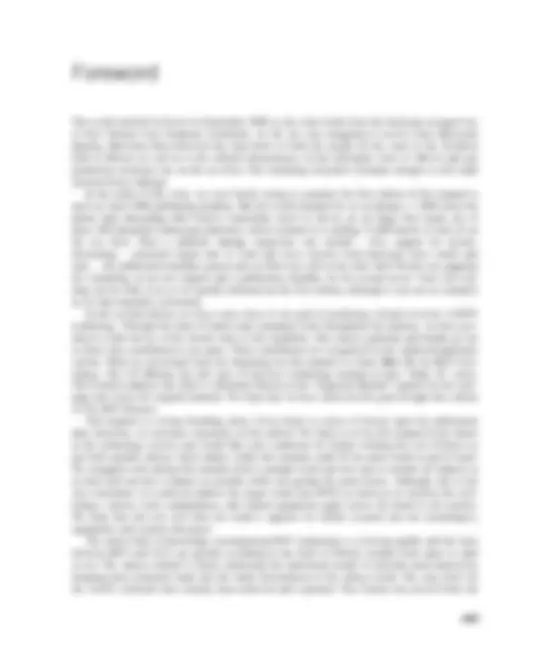
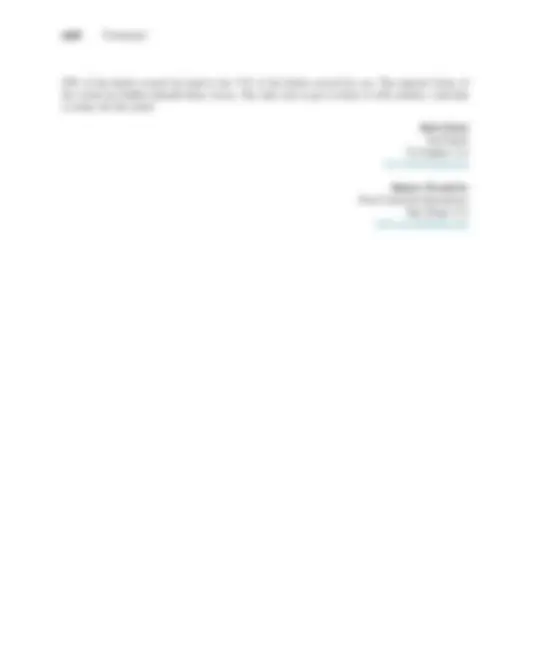
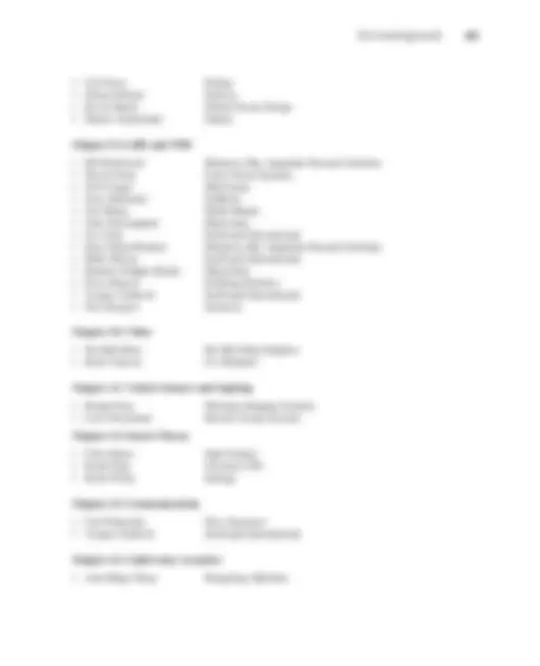
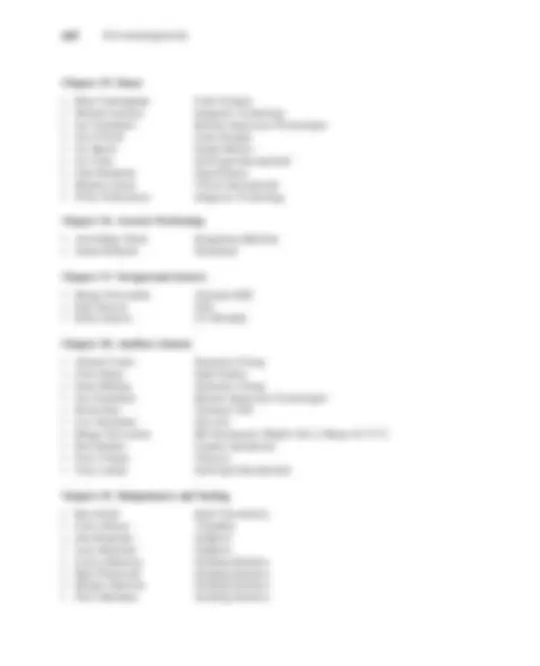
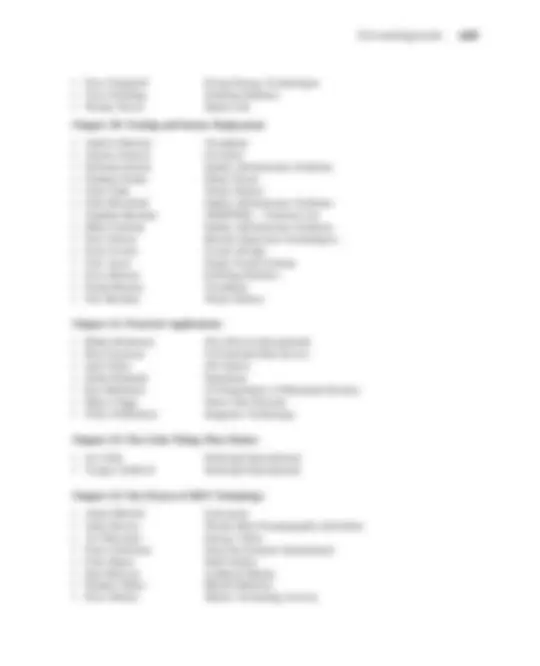
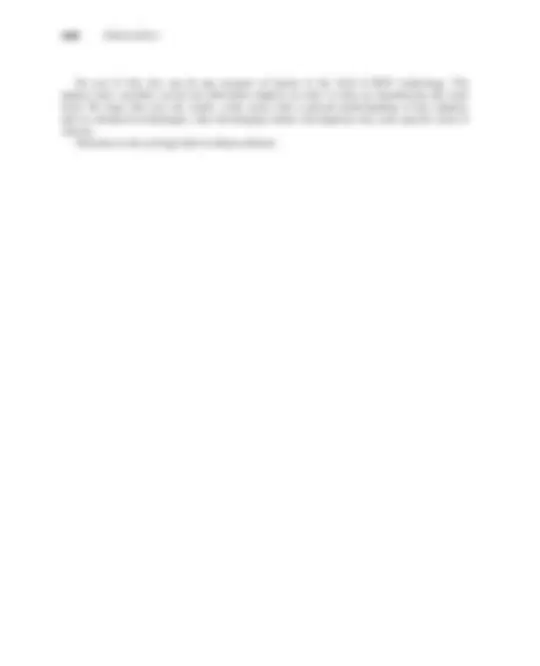
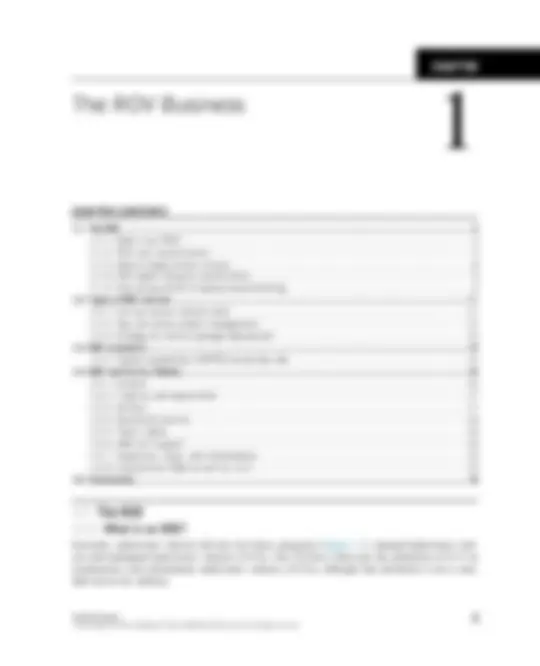
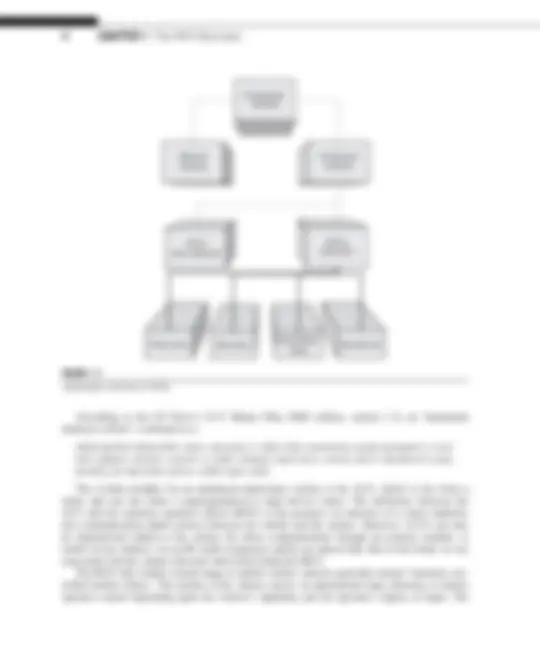
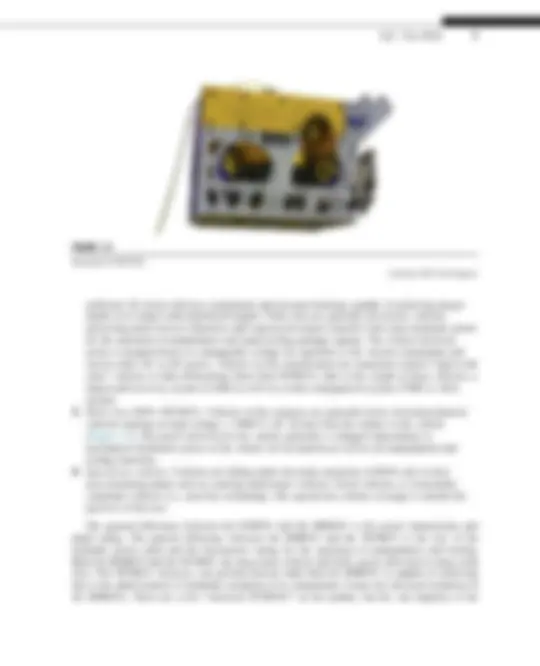
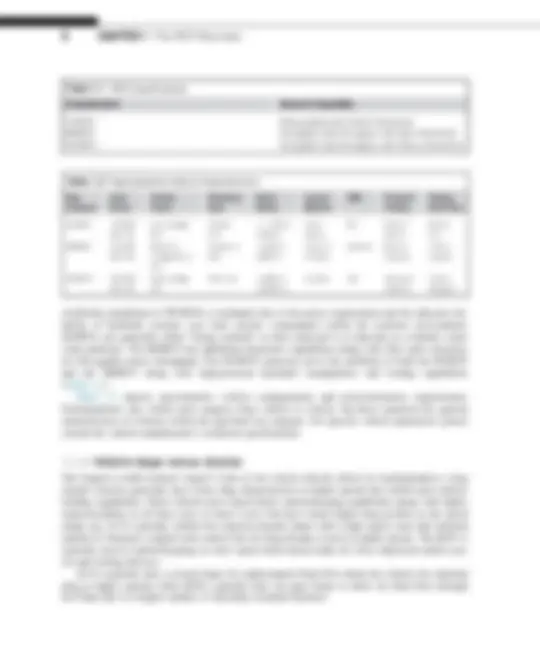
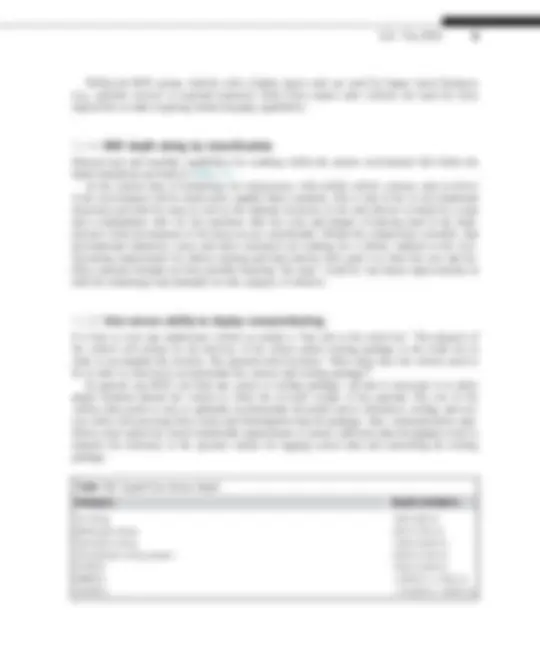
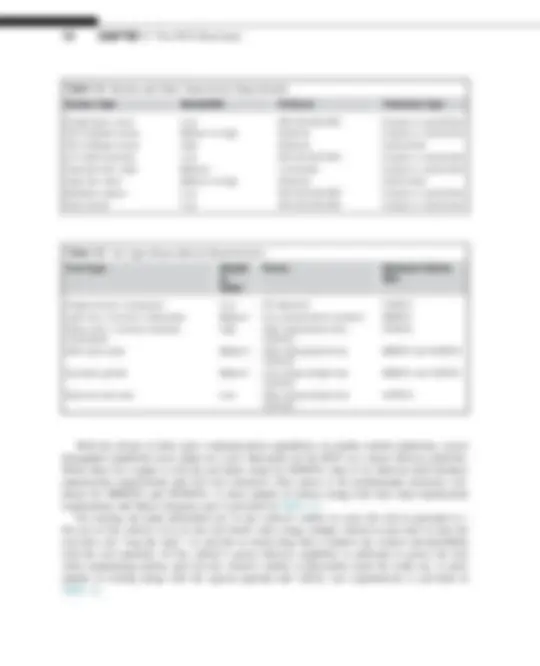
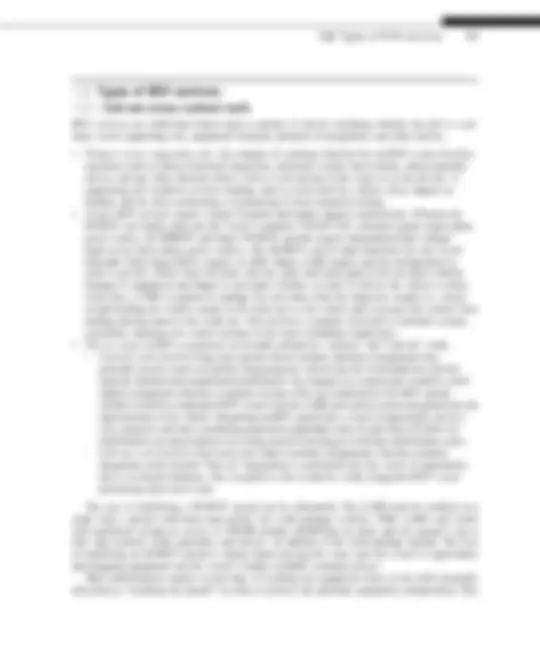
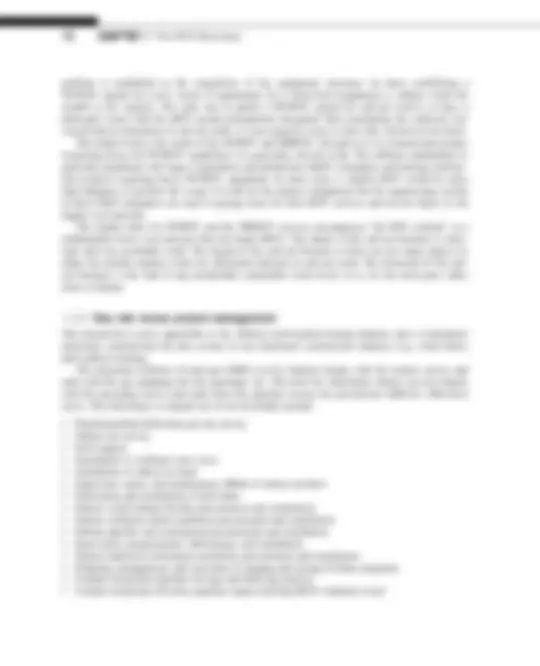
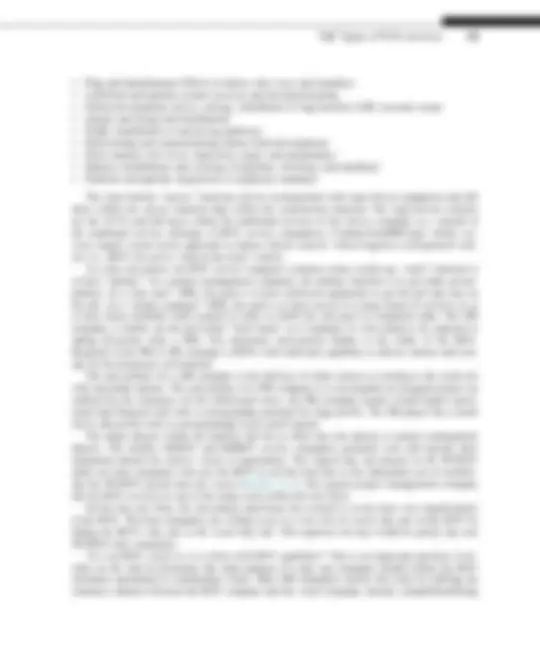
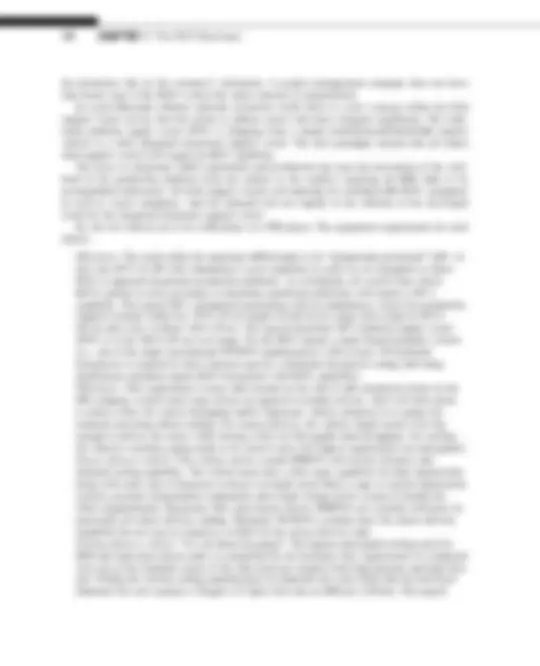
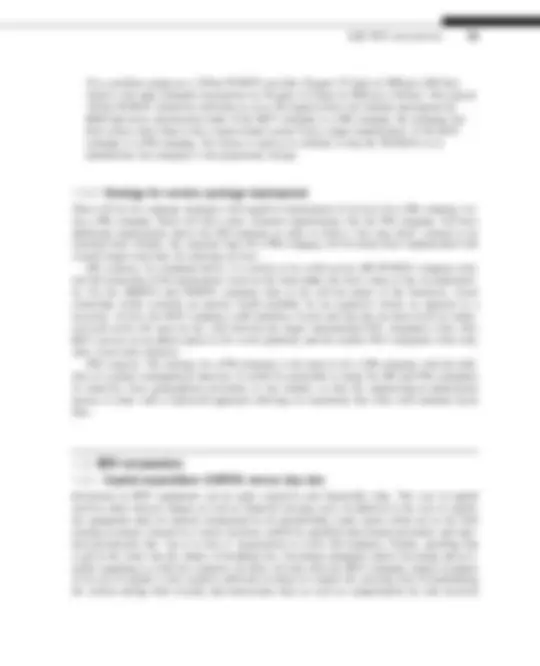
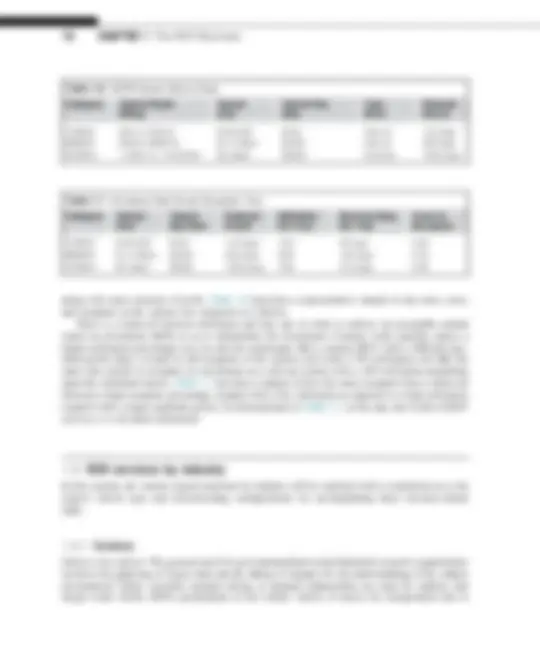
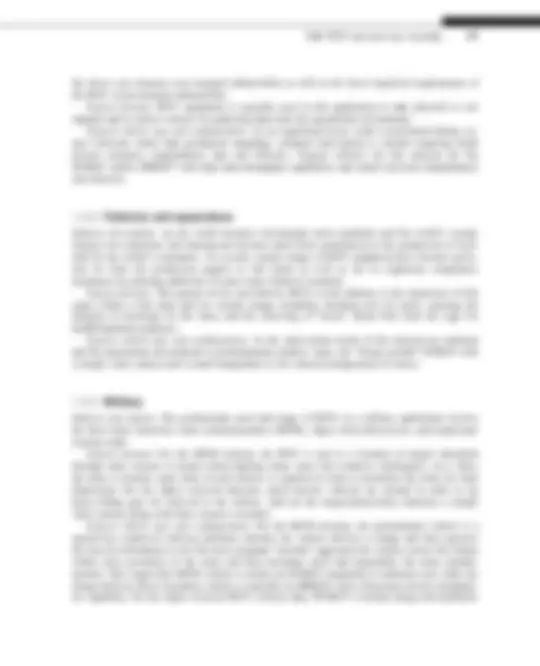
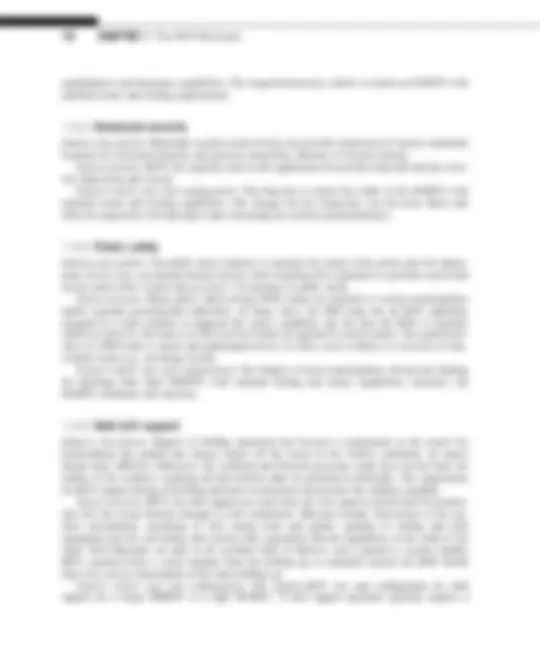
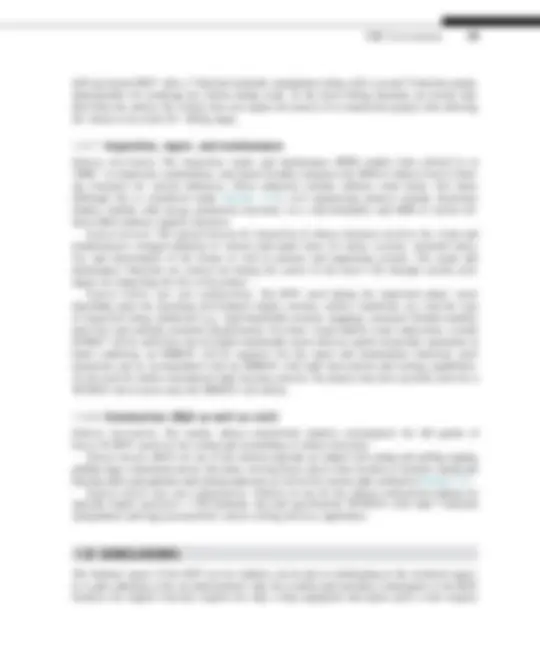
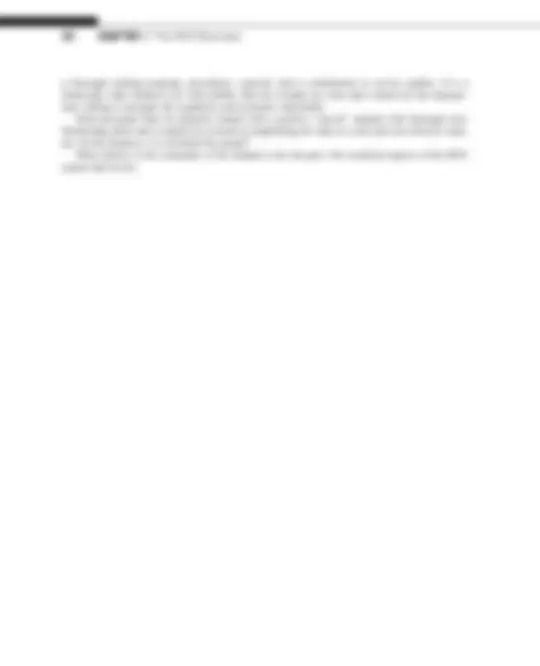
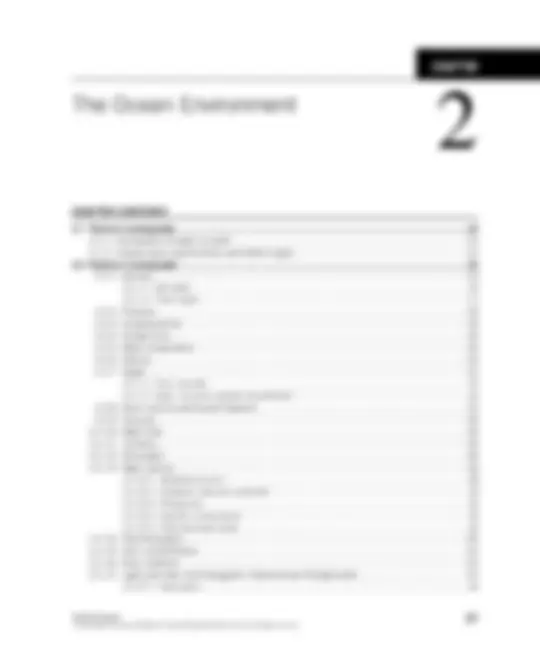
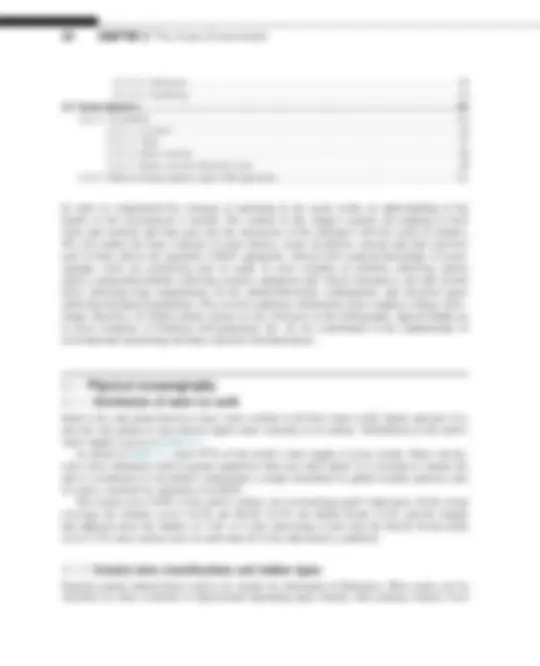
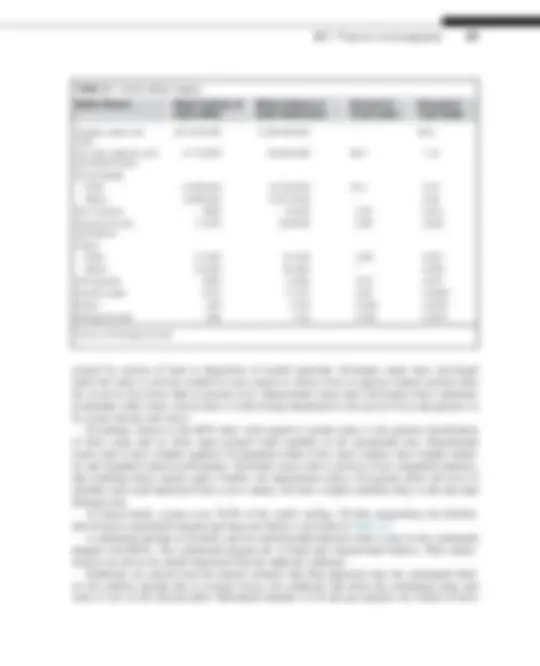
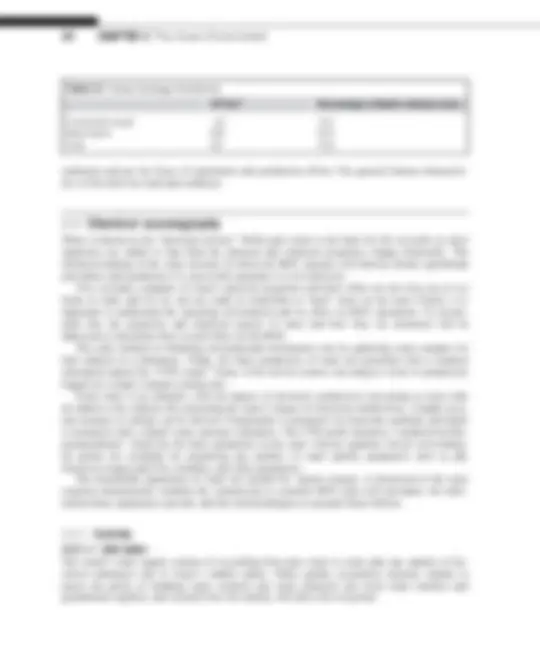
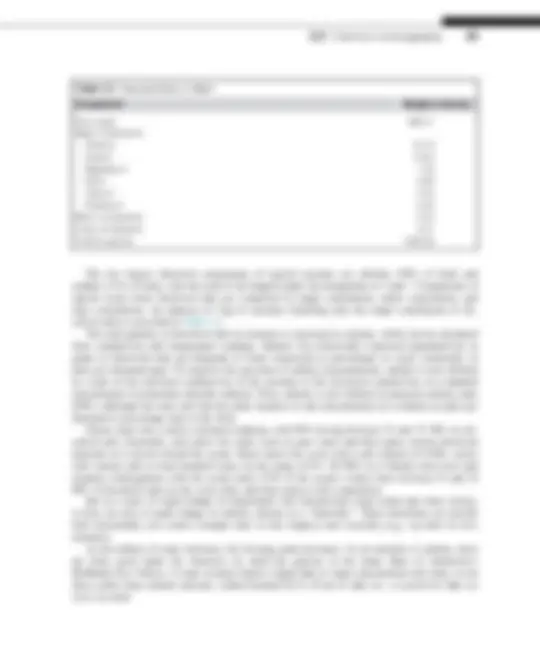
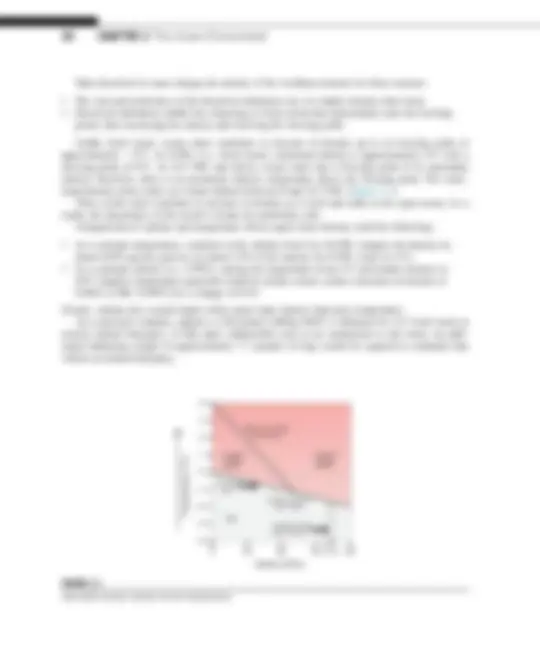
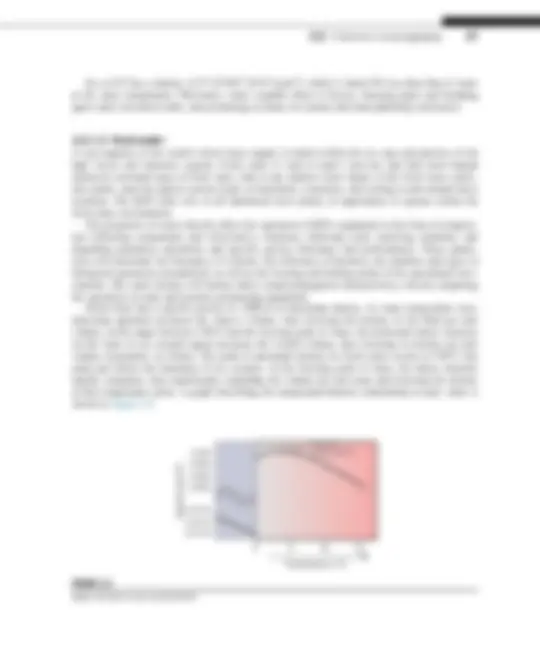
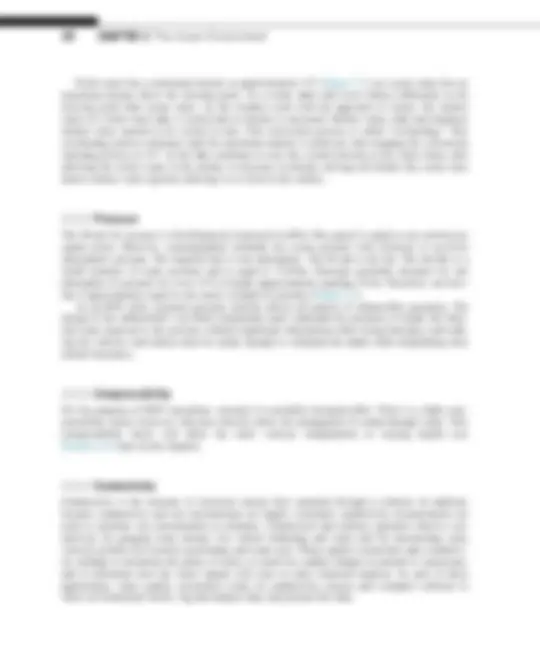
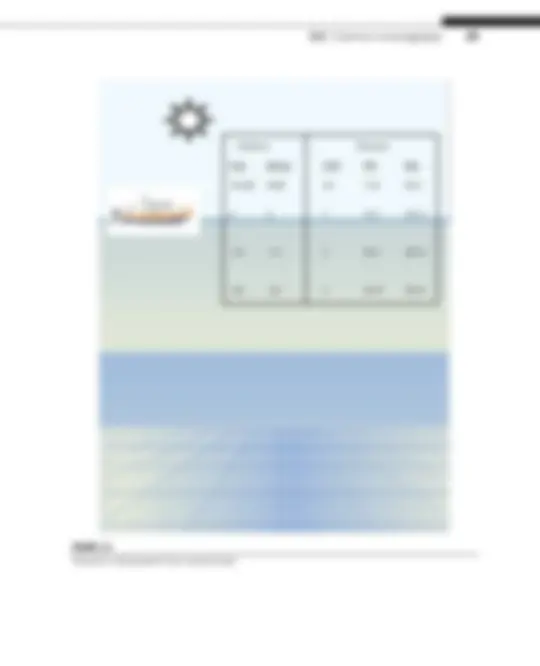
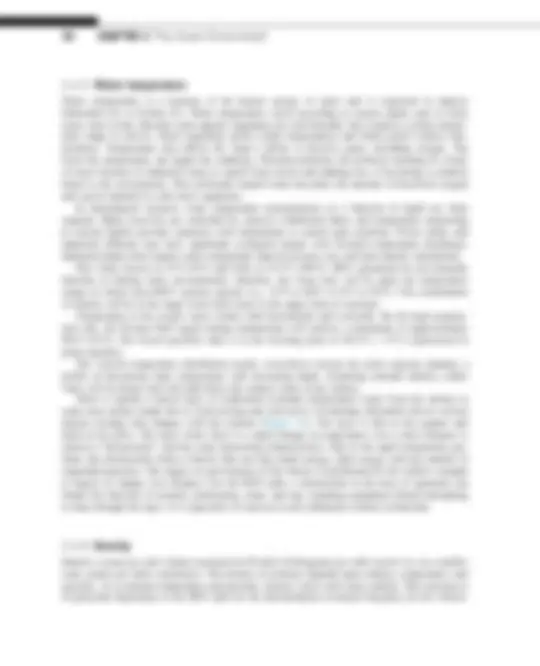
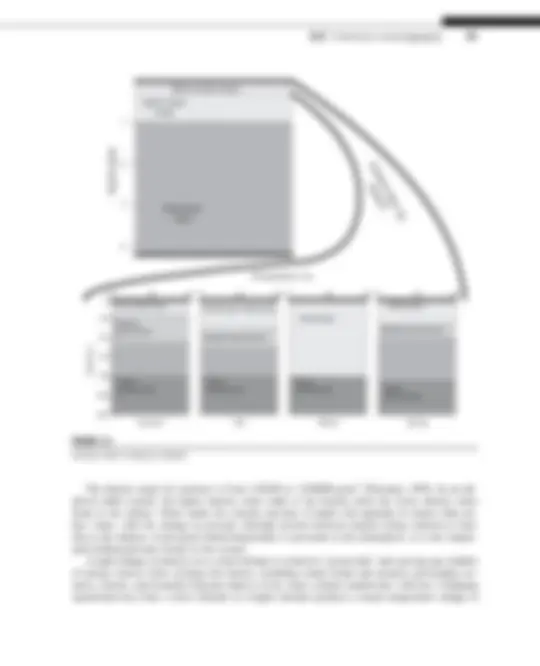

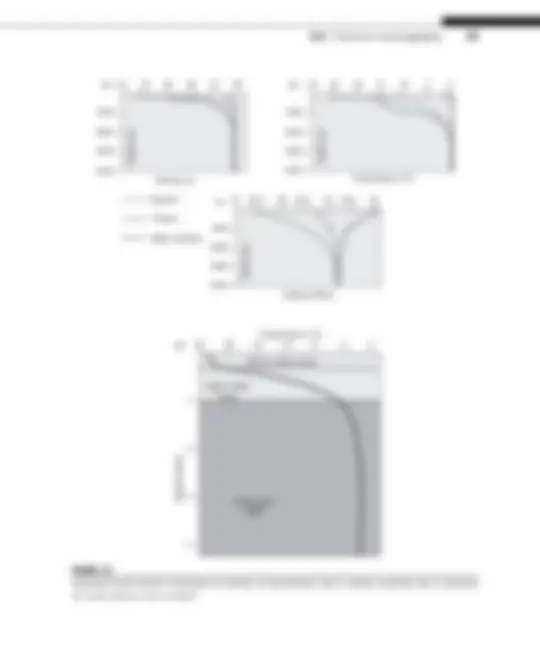
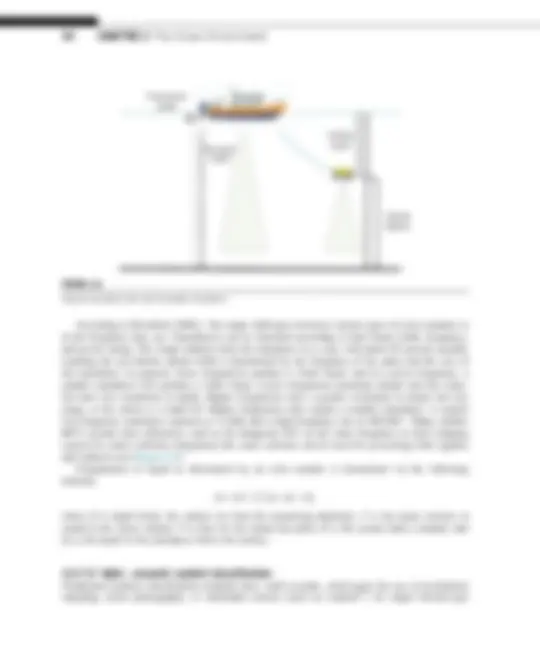
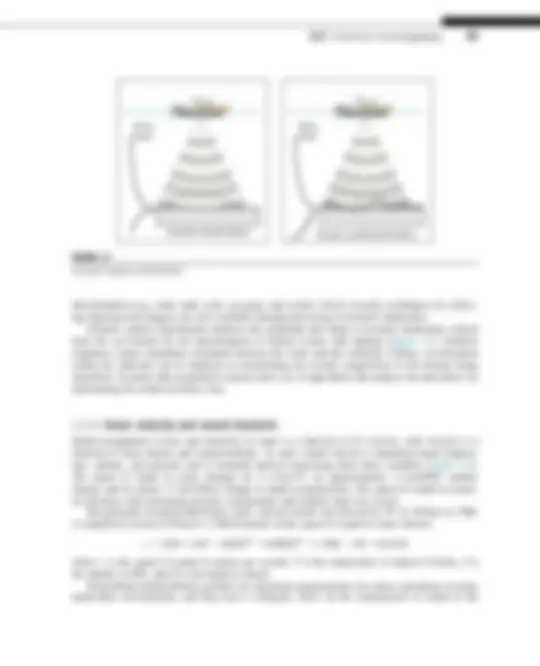
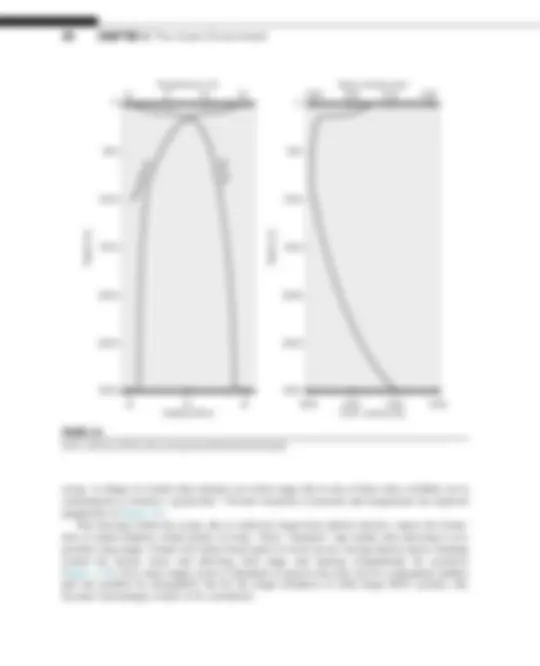
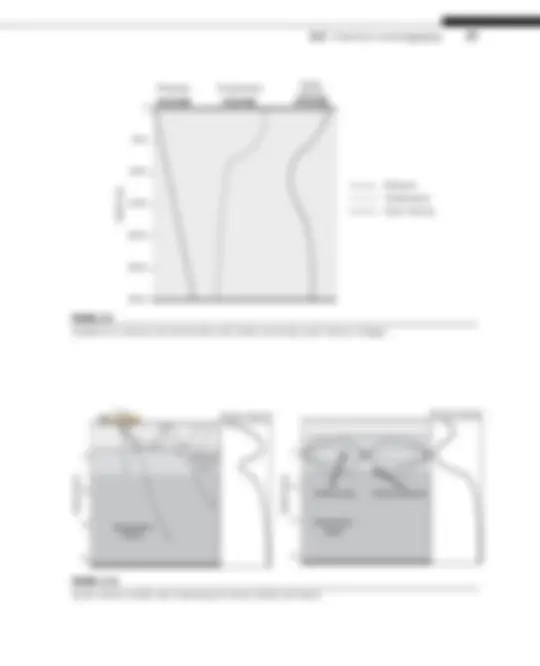
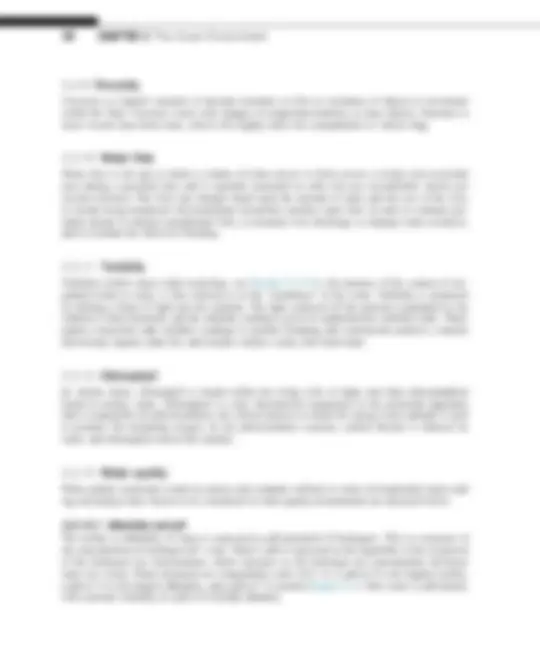
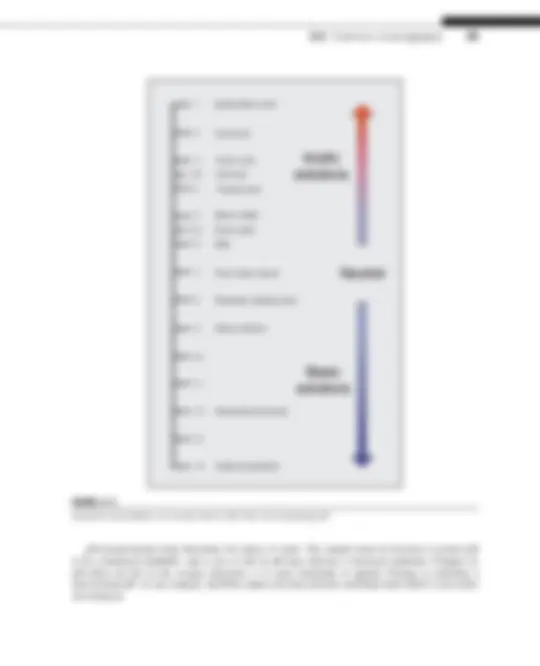
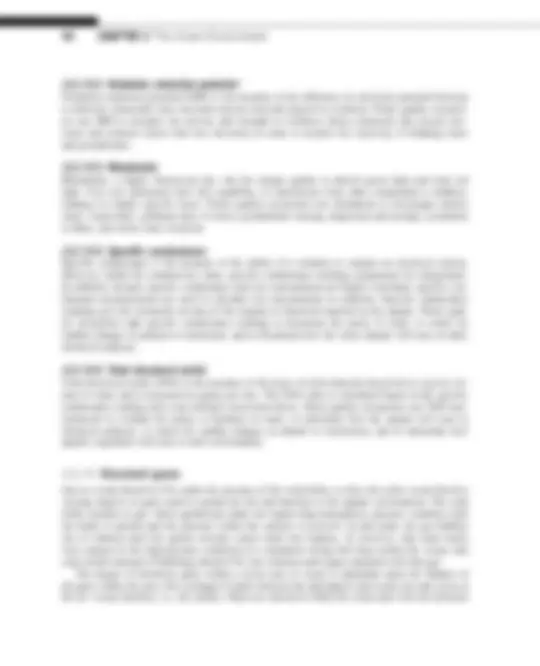
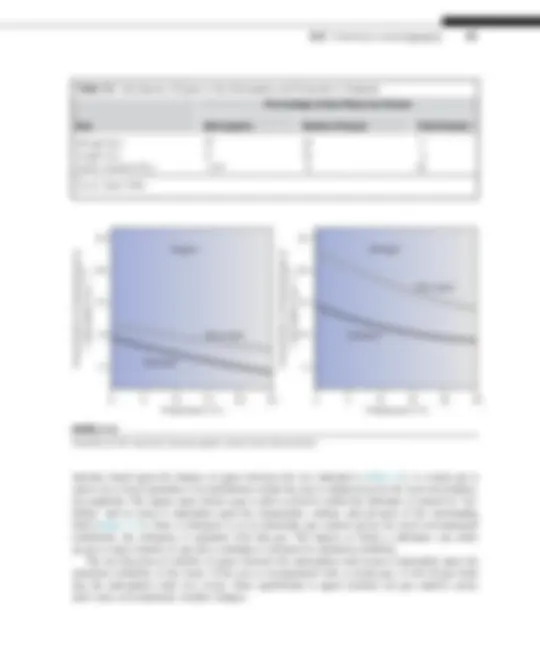

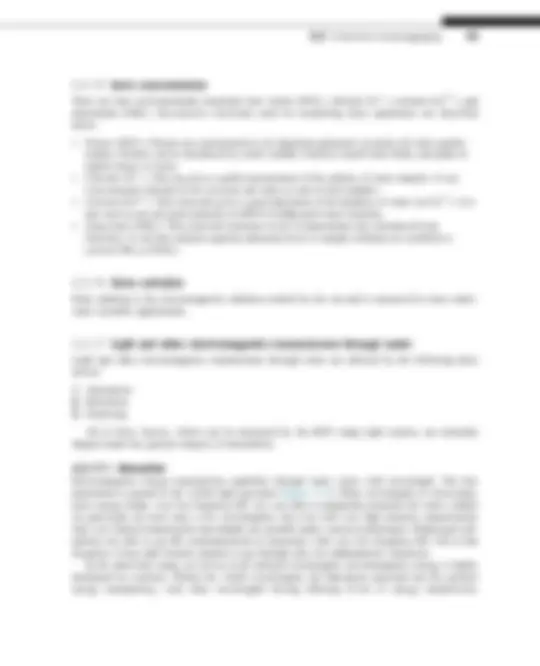
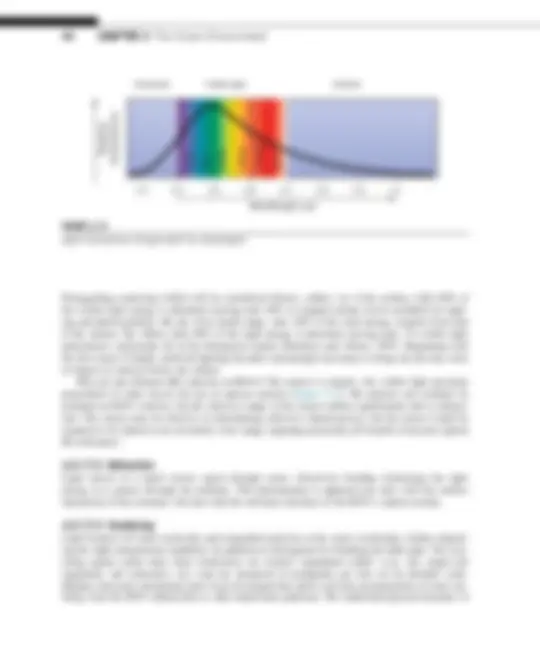
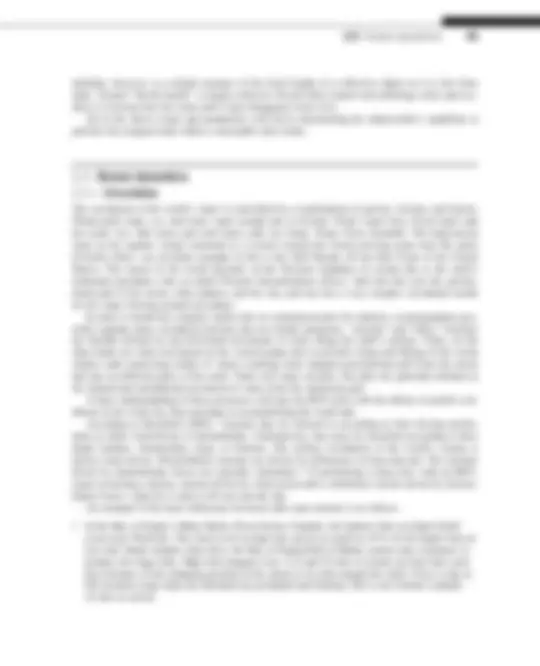
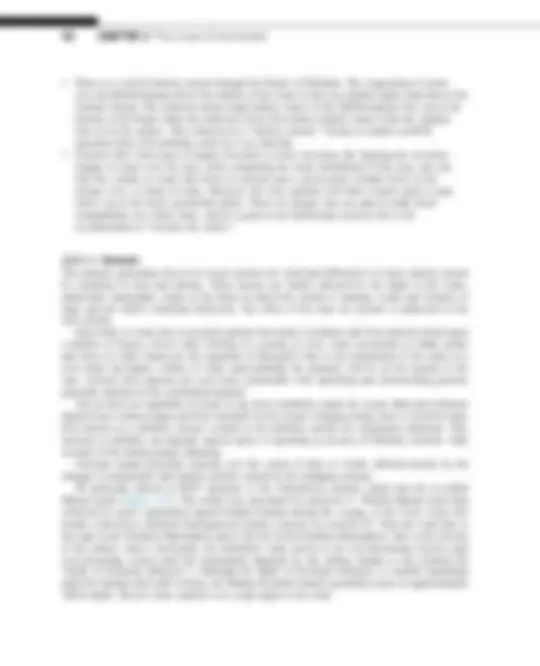
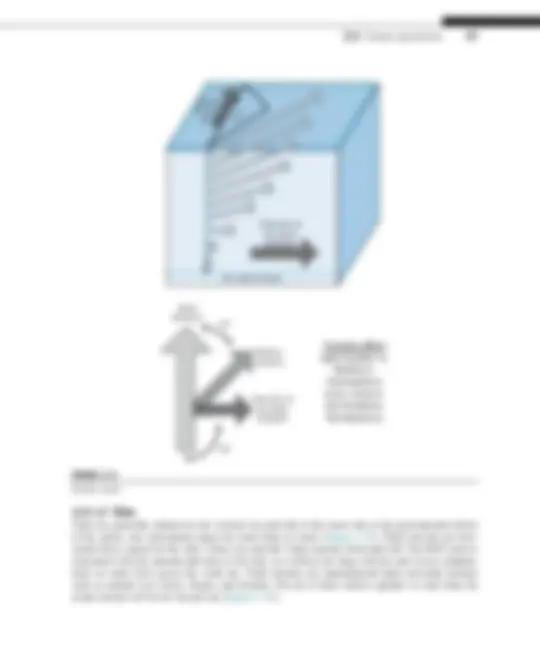
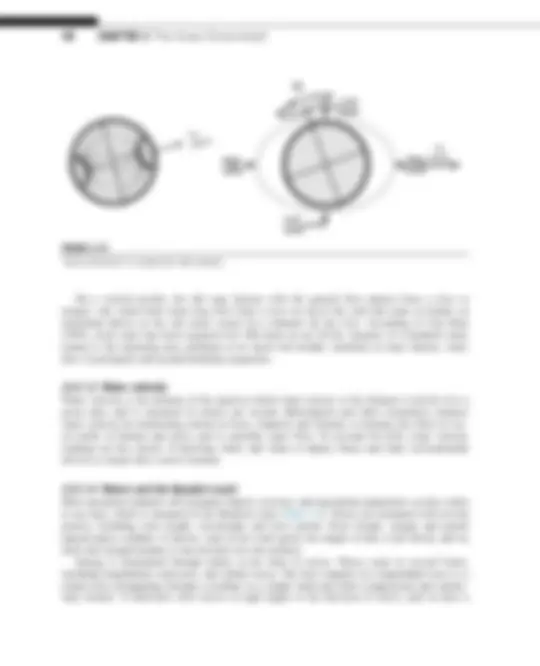
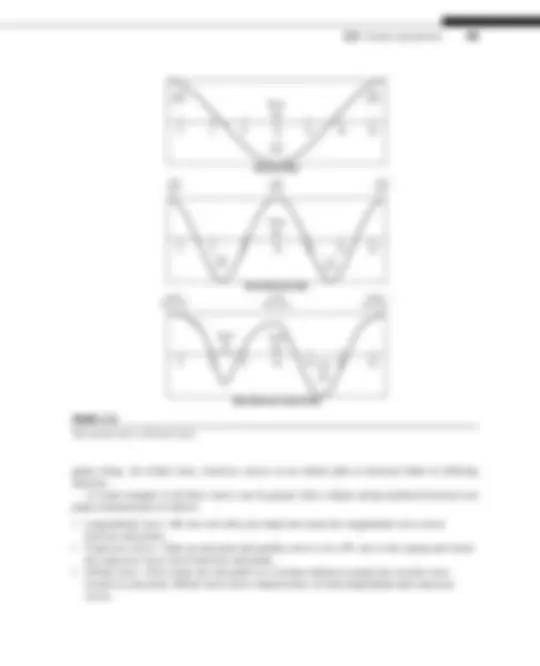
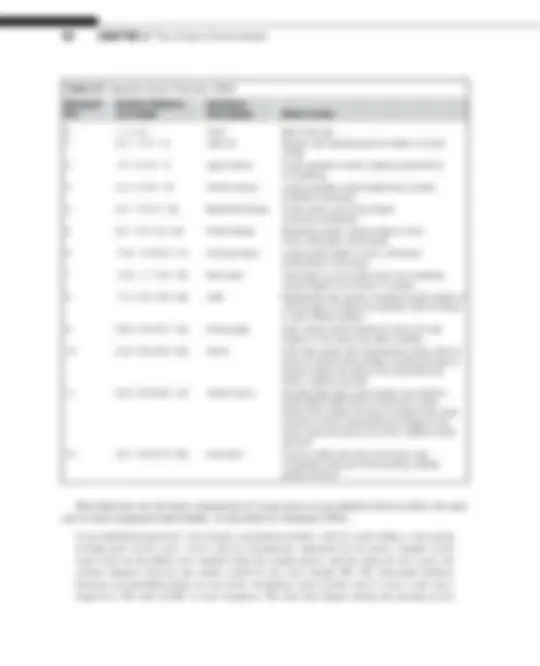
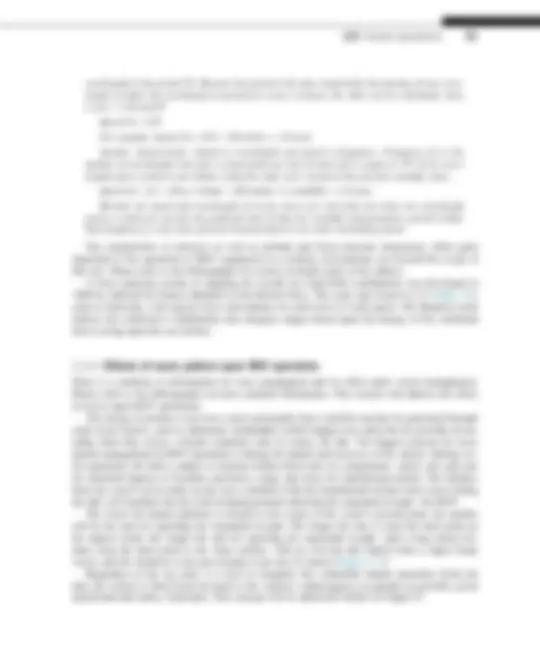
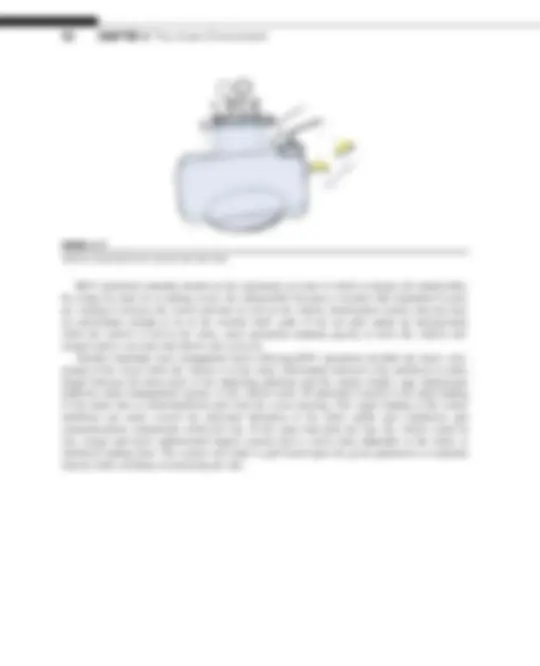
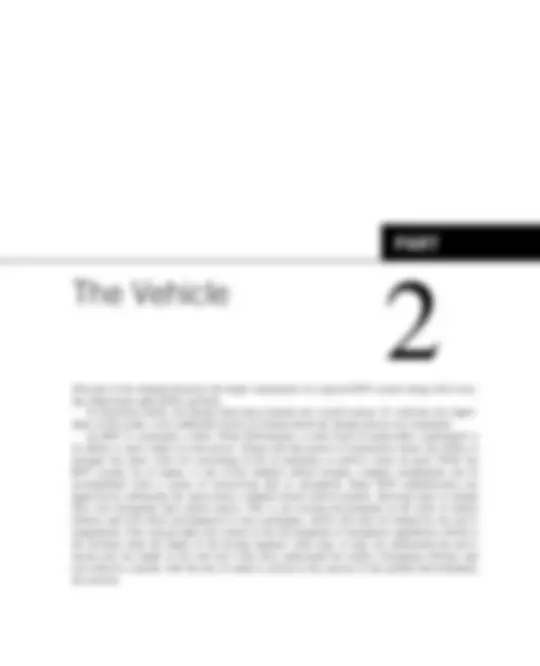
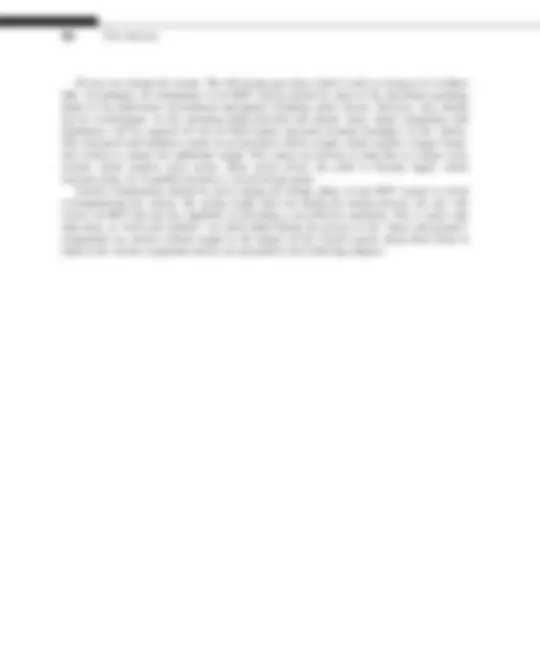
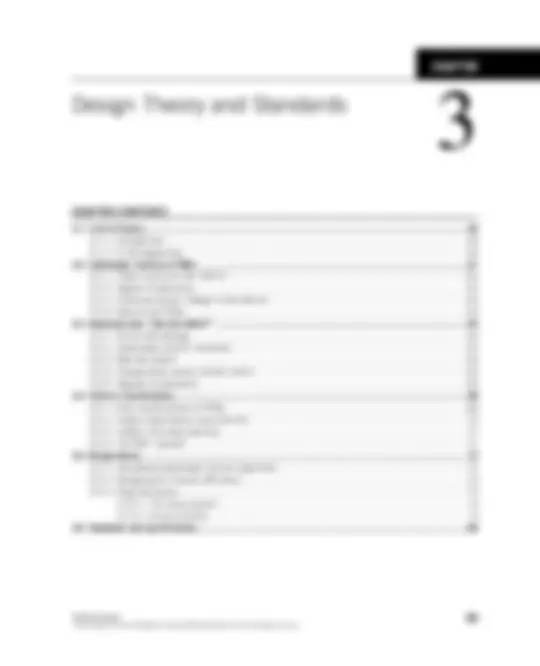
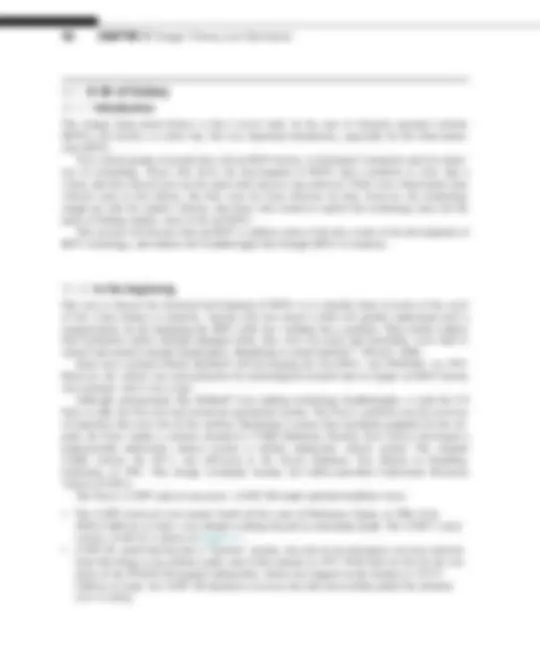
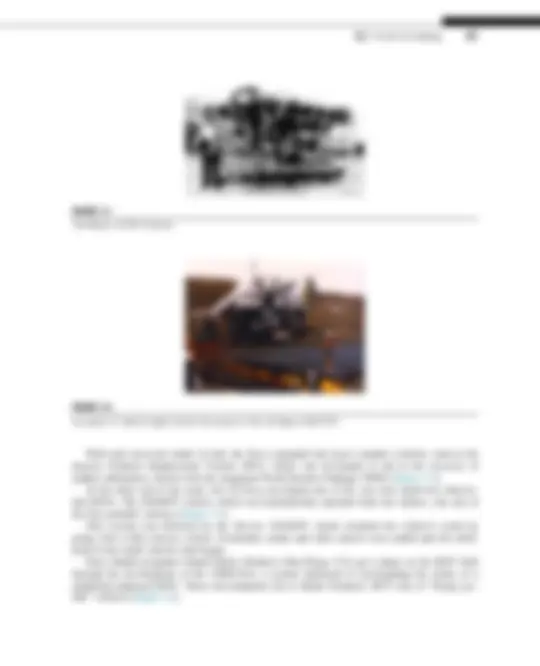
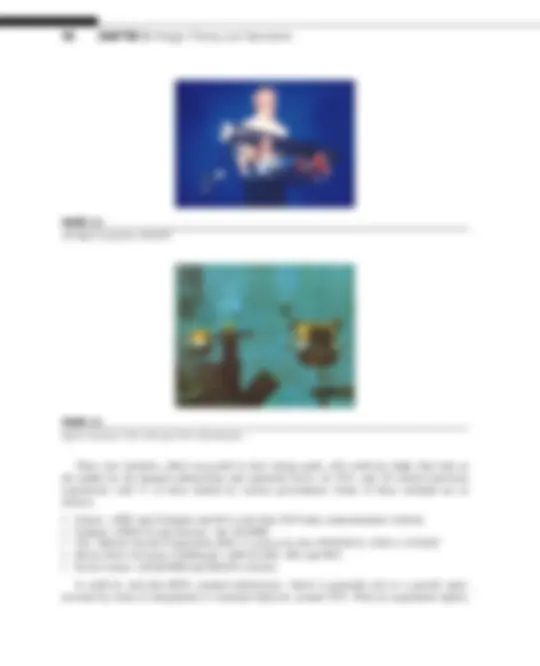
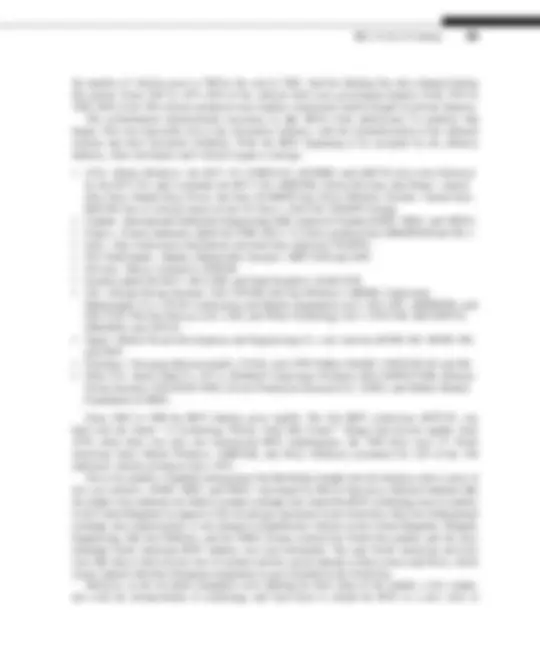
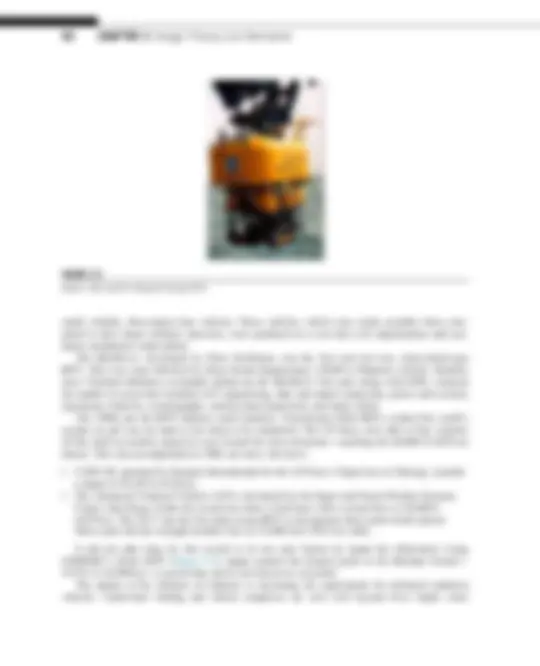
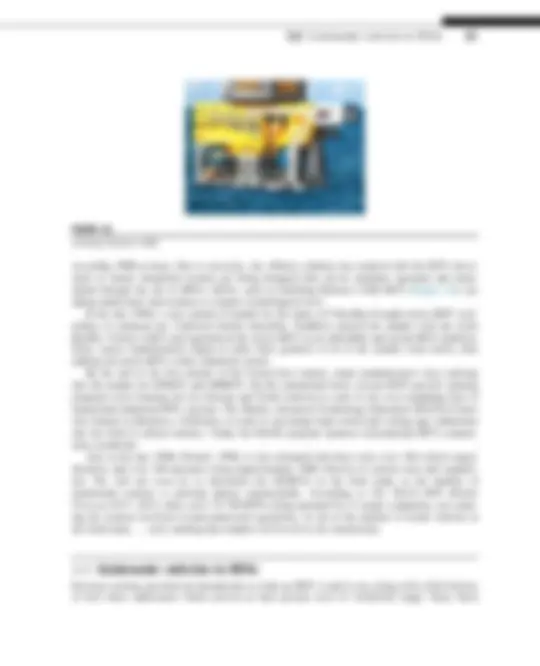
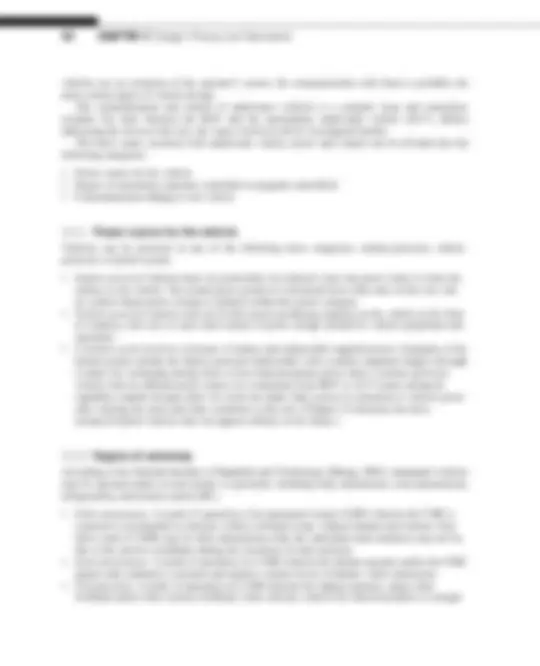
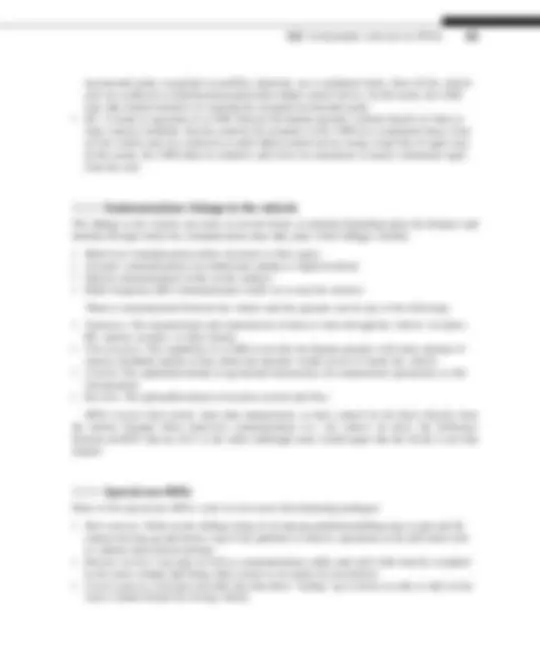
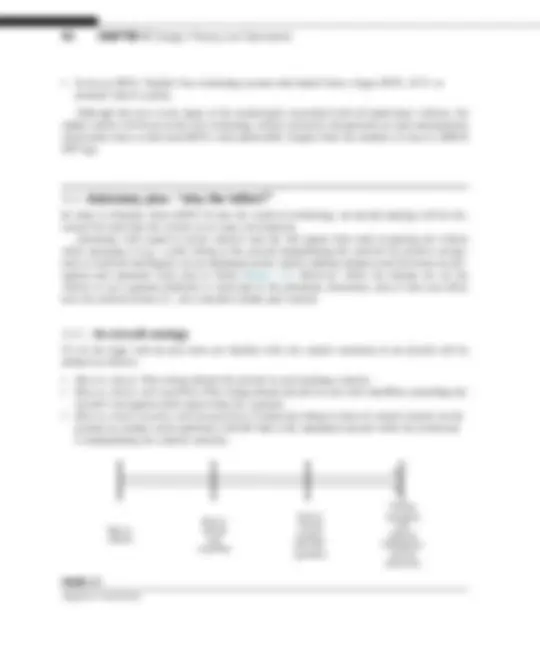
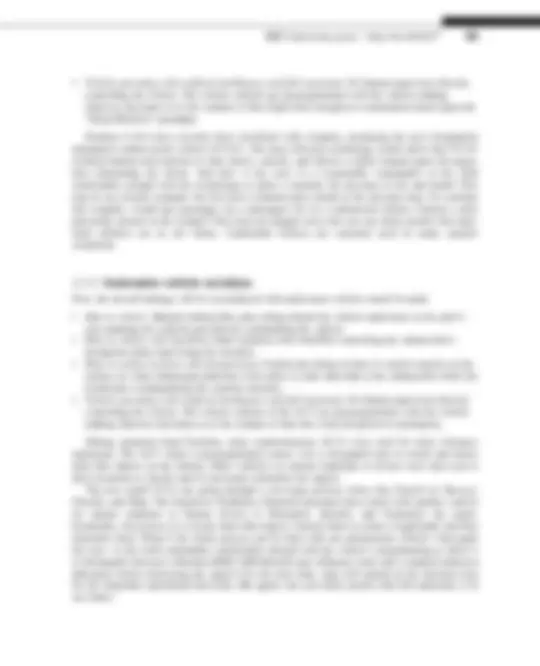
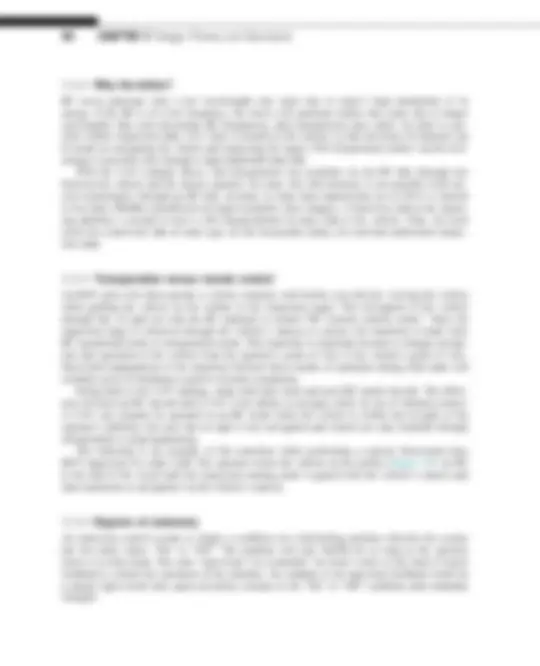
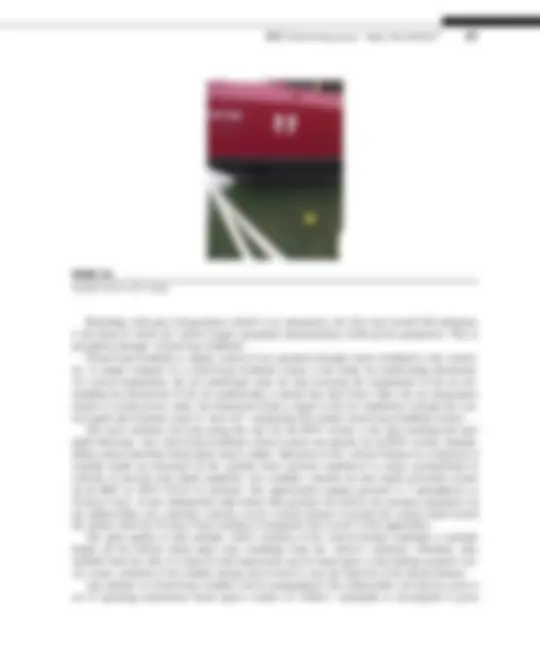
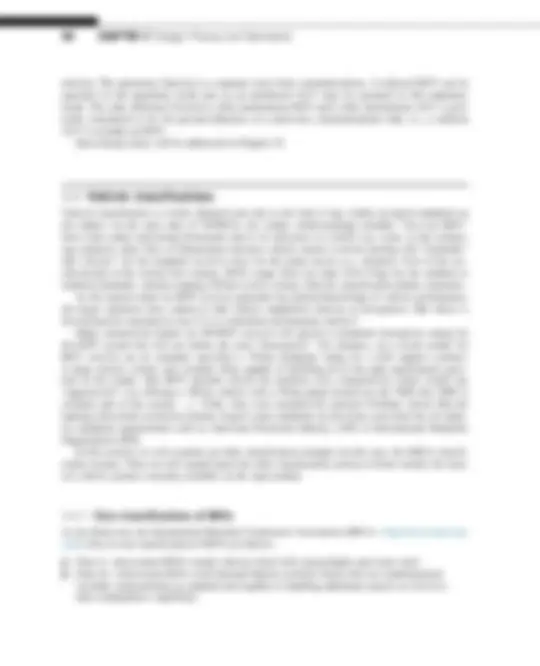
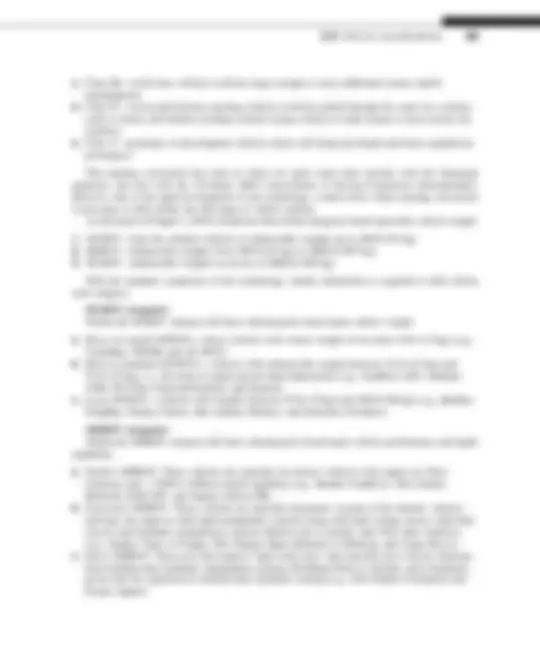
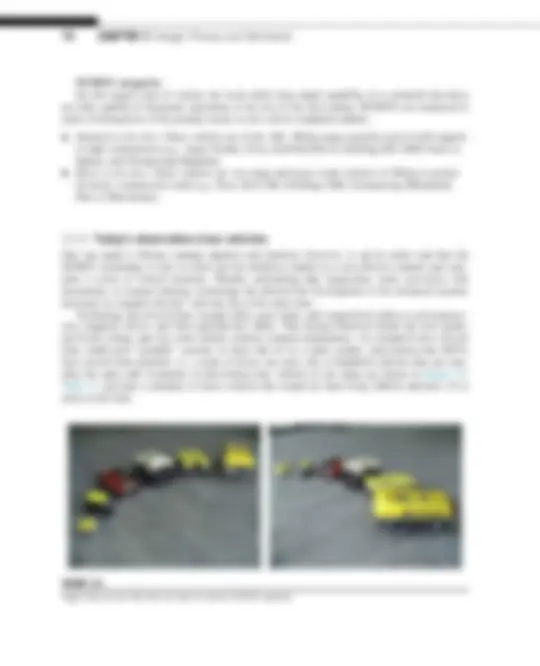
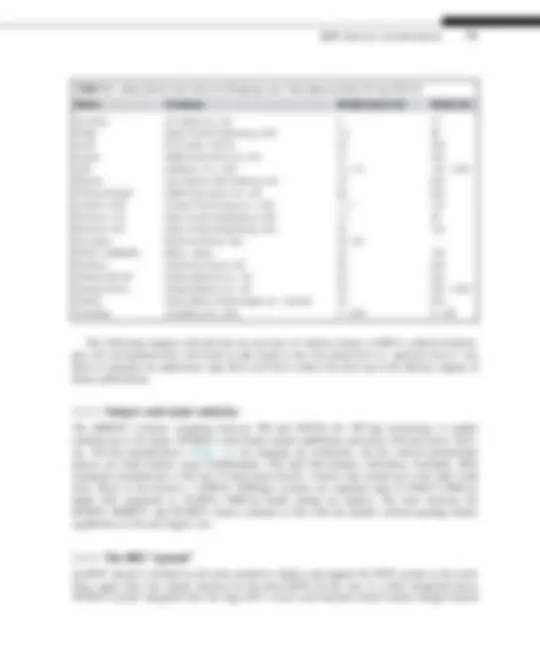
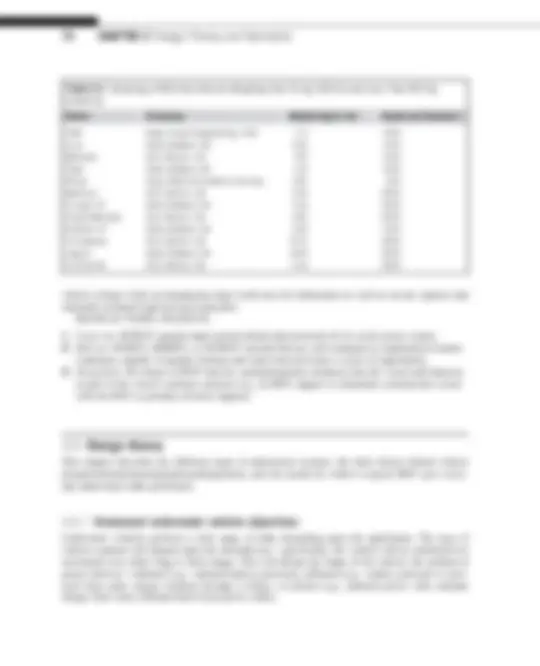

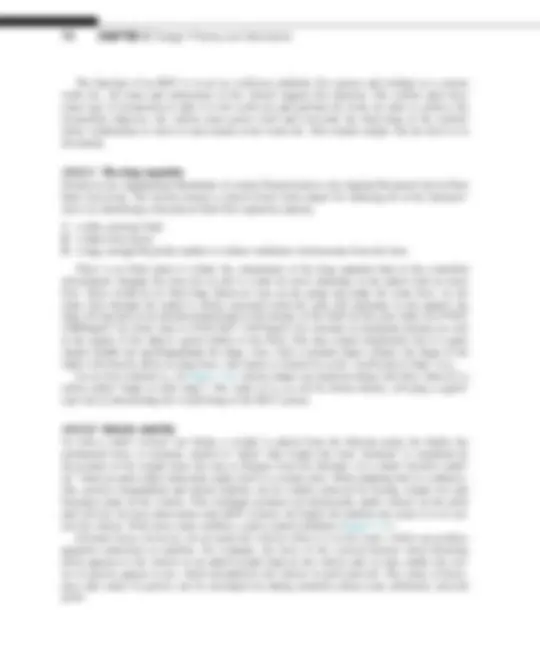
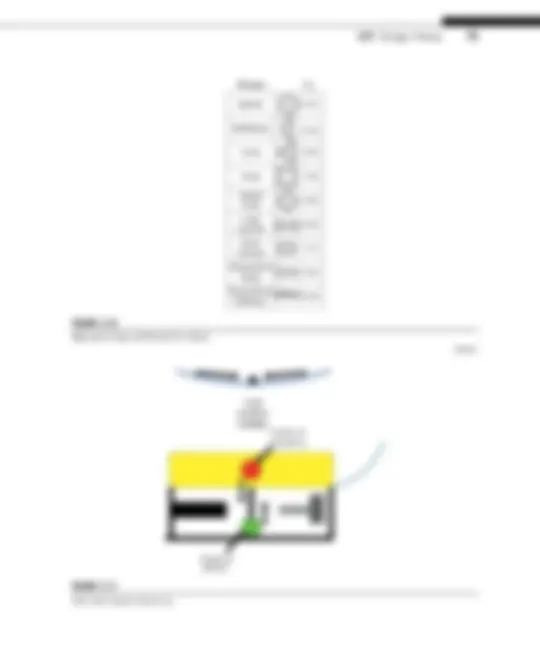
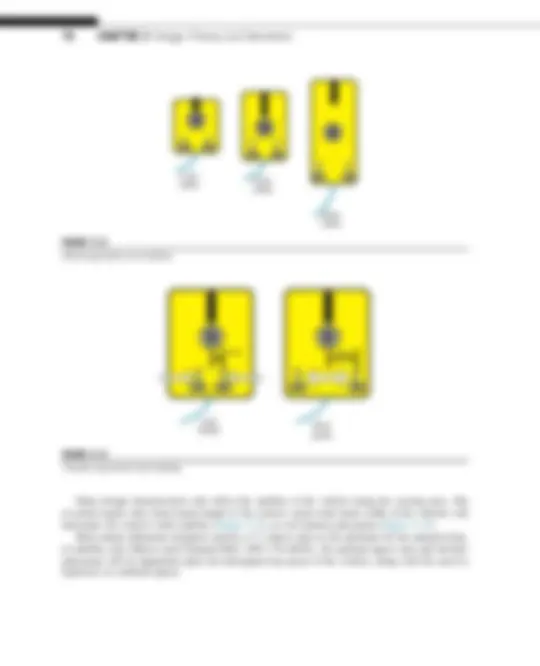
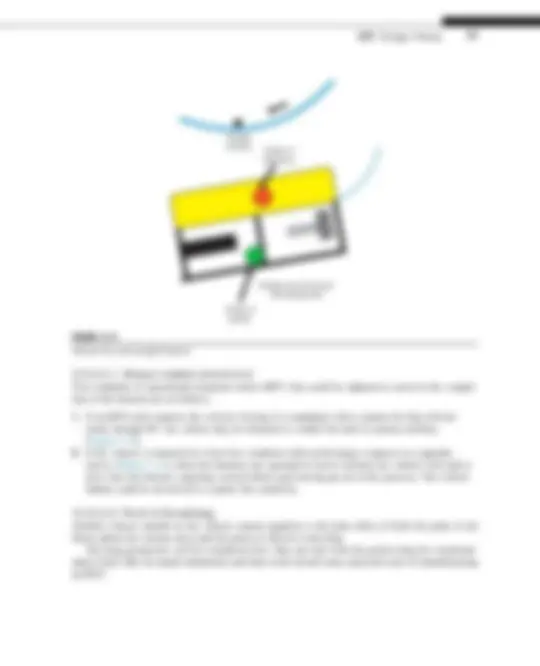
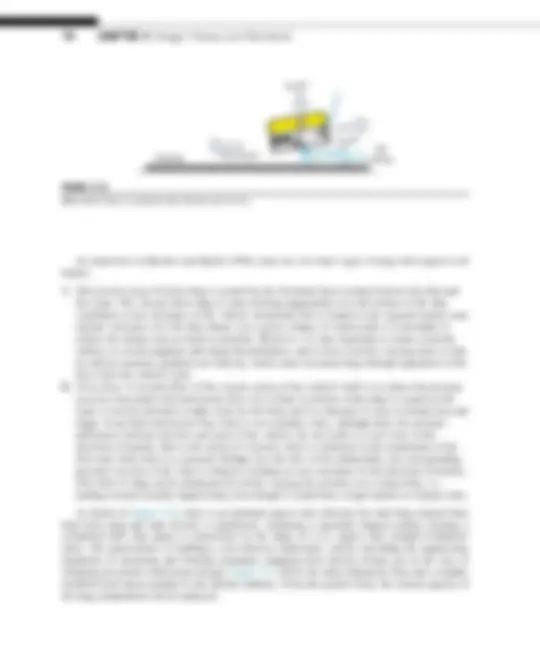
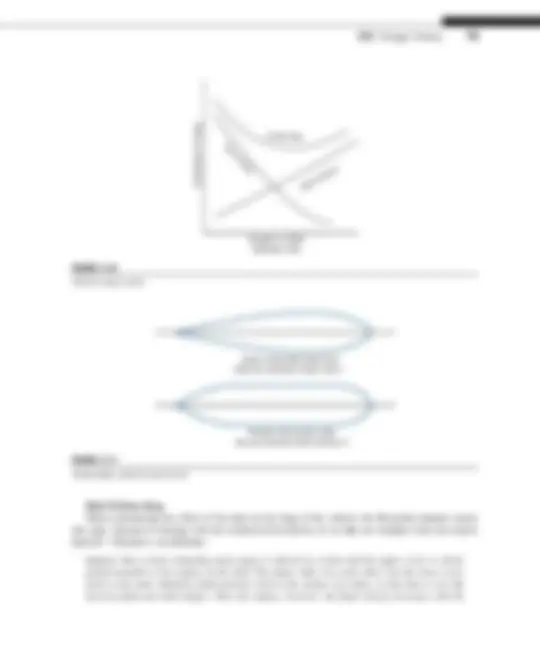
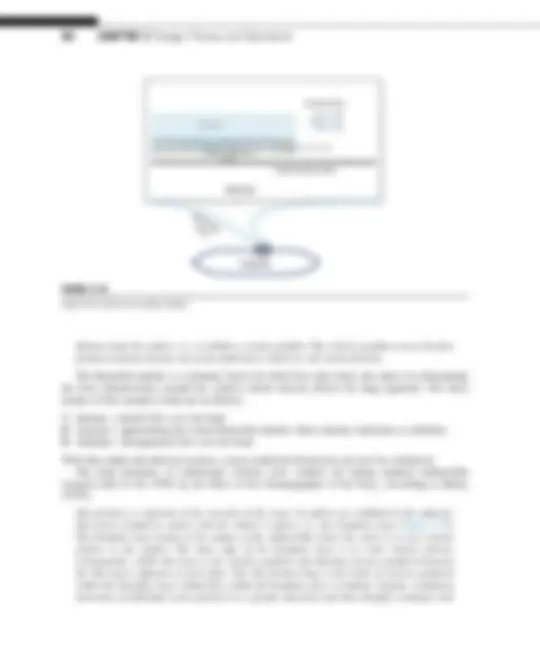
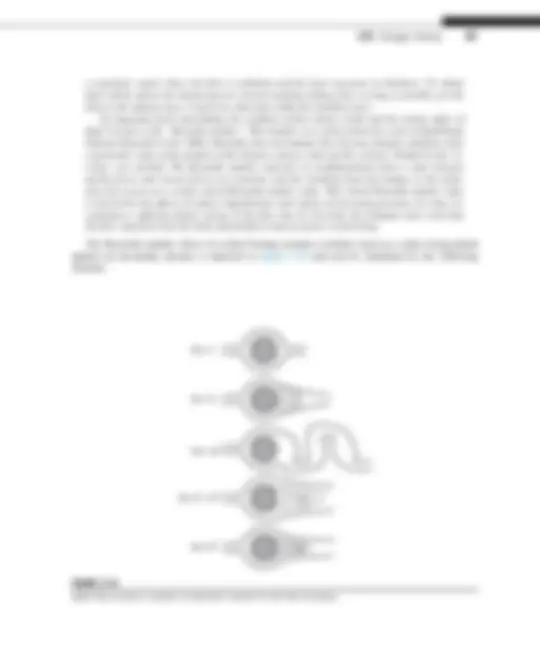
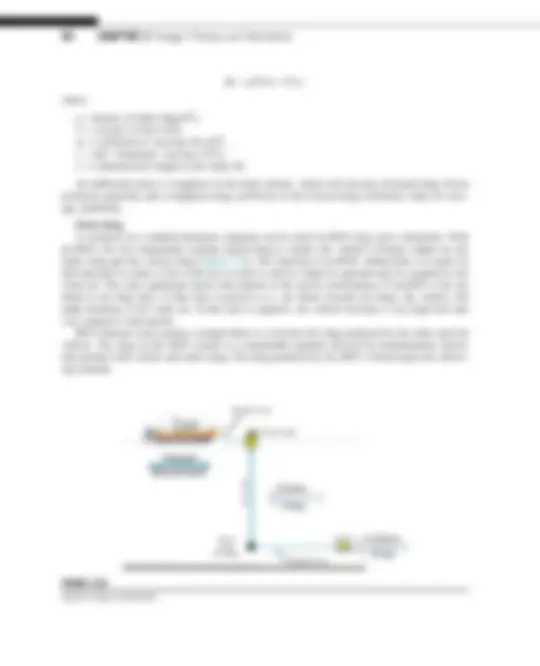
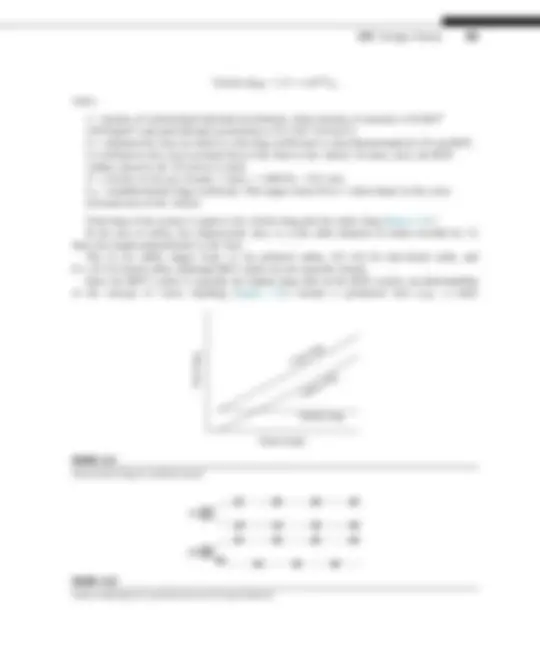
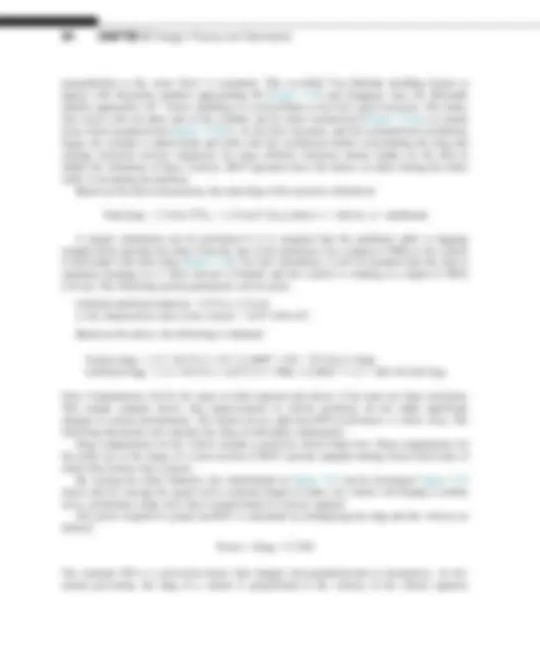
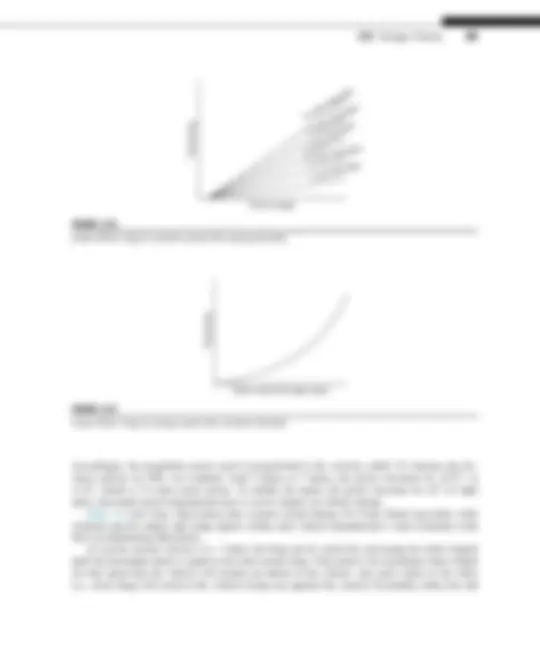
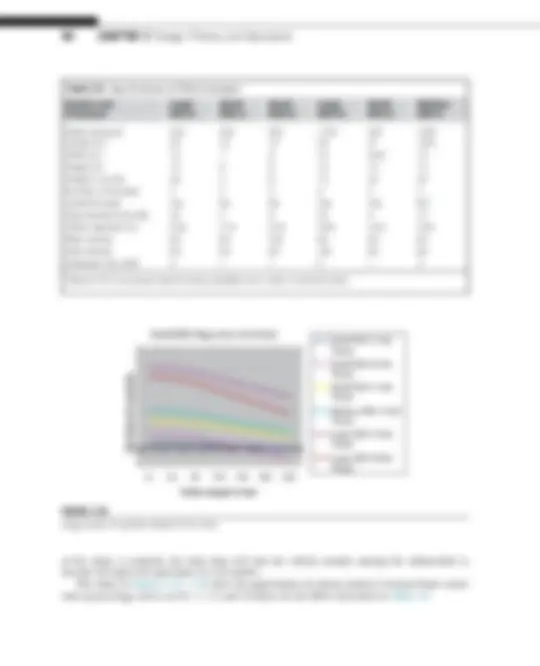
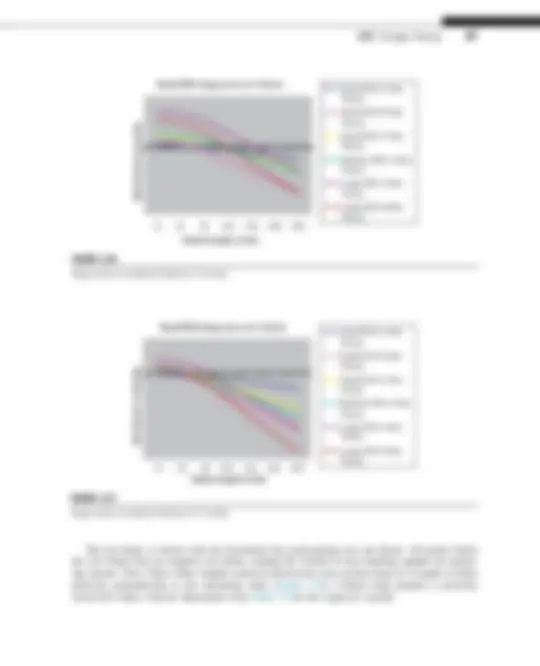
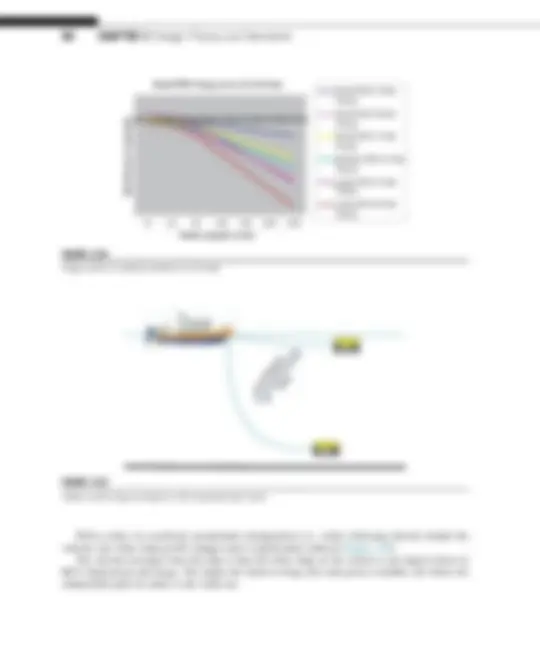
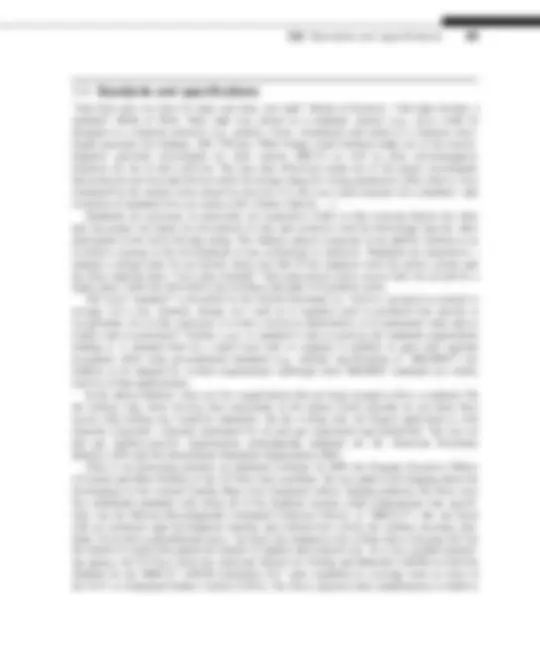
Estude fácil! Tem muito documento disponível na Docsity
Ganhe pontos ajudando outros esrudantes ou compre um plano Premium
Prepare-se para as provas
Estude fácil! Tem muito documento disponível na Docsity
Prepare-se para as provas com trabalhos de outros alunos como você, aqui na Docsity
Os melhores documentos à venda: Trabalhos de alunos formados
Prepare-se com as videoaulas e exercícios resolvidos criados a partir da grade da sua Universidade
Responda perguntas de provas passadas e avalie sua preparação.
Ganhe pontos para baixar
Ganhe pontos ajudando outros esrudantes ou compre um plano Premium
Comunidade
Peça ajuda à comunidade e tire suas dúvidas relacionadas ao estudo
Descubra as melhores universidades em seu país de acordo com os usuários da Docsity
Guias grátis
Baixe gratuitamente nossos guias de estudo, métodos para diminuir a ansiedade, dicas de TCC preparadas pelos professores da Docsity
This edition of The ROV Manual substantially expands upon the previous edition. This text is divided into five logical parts covering the industry and environment, the basics of ROV technology, payload sensors, intervention tooling as well as practical field applications. In the last chapter of the book, we look into the future in order to examine what industry analysts feel is the direction subsea technology is heading with a specific focus on the field of subsea robotics.
Tipologia: Manuais, Projetos, Pesquisas
Oferta por tempo limitado
Compartilhado em 20/06/2015
5
(5)2 documentos
1 / 676
Esta página não é visível na pré-visualização
Não perca as partes importantes!
Em oferta
AMSTERDAM • BOSTON • HEIDELBERG • LONDON NEW YORK • OXFORD • PARIS • SAN DIEGO SAN FRANCISCO • SINGAPORE • SYDNEY • TOKYO Butterworth-Heinemann is an imprint of Elsevier
Foreword
The world watched in horror in September 2005 as the video feeds from the hurricane-ravaged city of New Orleans were broadcast worldwide. As the city was struggling to recover from Hurricane Katrina, Hurricane Rita delivered the final blow to both the people on the coast of the Northern Gulf of Mexico as well as to the oilfield infrastructure. In the aftermath, close to 200 oil and gas production structures lay on the sea floor. The remaining structures fortunate enough to still stand incurred heavy damage. In the midst of this crisis, we were busily trying to complete the first edition of this manual to meet an April 2006 publishing deadline. But the world changed for us on January 1, 2006 when the phone rang demanding Bob Christ’s immediate travel to survey an oil barge that struck one of those 200 unmarked submerged platforms, which resulted in it spilling 72,000 barrels of fuel oil on the sea floor. Then a platform damage inspection was needed... dive support for decom- missioning... structural repairs due to wind and wave stresses from hurricane force winds and seas... the publication deadline passed and yet Bob was still in the field. Bob Wernli was juggling his consulting, at-sea test support and a publication deadline for his second novel. Time was run- ning out for both of us so we quickly buttoned up the first edition, although it was not as complete as we had originally envisioned. In this second edition, we have come closer to our goal of producing a broad overview of ROV technology. Through the help of leaders and companies from throughout the industry, we have pro- duced a solid survey of the current state of this capability. Our sincere gratitude and thanks go out to those who contributed to our quest. These contributors are recognized in the Acknowledgements section. What we envisioned from the beginning for this manual is a basic How To for ROV tech- nology. The US Military has this type of top-level technology manual in their “Dash 10” series. The aviation industry has what is commonly known as the “Jeppesen Manual” (named for the com- pany that wrote the original manual). We hope that we have achieved this goal through this edition of The ROV Manual. This manual is a living breathing entity. Every book is a piece of history upon the publication date; therefore, we welcome comments on this edition. We hope to revise this manual in the future as the technology evolves and would like your comments for further refining this text if/when we put forth another edition. Each subject within this manual could fill an entire book in and of itself. We struggled with editing this manual (with a nominal word and text cap) to include all subjects in as short and succinct a manner as possible while still getting the point across. Although, due to the size constraints, we could not address the larger work-class ROVs as much as we desired, the tech- nology, sensors, tools, manipulators, and related equipment apply across the board to all systems. We hope that this text will whet the reader’s appetite for further research into the technologies, equipment, and systems discussed. The entire body of knowledge encompassing ROV technology is evolving rapidly and the lines between ROV and AUV are quickly occluding as the field of robotics morphs from space to land to sea. The subsea oilfield is firmly embracing the land-based model of network interconnectivity bringing man (remotely) back into the harsh environment of the subsea world. The easy finds for the world’s minerals have already been achieved and exploited. The frontier has moved from the
29% of the Earth covered by land to the 71% of the Earth covered by sea. The mineral riches of the world are hidden beneath those waves. The only way to get to them is with robotics. And that is where the fun starts!
Bob Christ SeaTrepid Covington, LA www.SeaTrepid.com
Robert Wernli Sr First Centurion Enterprises San Diego, CA www.wernlibooks.com
Chapter 2: The Ocean Environment
Chapter 3: Theory and Standards
Chapter 4: Vehicle Control and Simulation
Chapter 5: Vehicle Design and Stability
Chapter 6: Thrusters
Chapter 7: Power and Telemetry
Chapter 8: Cables and Connectors
Chapter 9: LARS and TMS
Chapter 10: Video
Chapter 11: Vehicle Sensors and Lighting
Chapter 12: Sensor Theory
Chapter 13: Communications
Chapter 14: Underwater Acoustics
Chapter 20: Tooling and Sensor Deployment
Chapter 21: Practical Applications
Chapter 22: The Little Things That Matter
Chapter 23: The Future of ROV Technology
No text of this size can do any measure of justice to the field of ROV technology. The authors have carefully carved out individual subjects in order to form an introduction into each field. We hope that you, the reader, come away with a general understanding of this industry and its advanced technologies, thus encouraging further investigation into your specific field of interest. Welcome to the exciting field of subsea robotics!
CHAPTER
The ROV Business
CHAPTER CONTENTS
1.1 The ROV ........................................................................................................................................... 1.1.1 What is an ROV?........................................................................................................... 3 1.1.2 ROV size classifications ................................................................................................ 5 1.1.3 Vehicle shape versus mission......................................................................................... 8 1.1.4 ROV depth rating by classification.................................................................................. 9 1.1.5 Size versus ability to deploy sensors/tooling .................................................................... 9 1.2 Types of ROV services ..................................................................................................................... 1.2.1 Call out versus contract work ....................................................................................... 11 1.2.2 Day rate versus project management ............................................................................ 12 1.2.3 Strategy for service package deployment ...................................................................... 15 1.3 ROV economics............................................................................................................................... 1.3.1 Capital expenditure (CAPEX) versus day rate ................................................................. 15 1.4 ROV services by industry ................................................................................................................. 1.4.1 Science ..................................................................................................................... 16 1.4.2 Fisheries and aquaculture ........................................................................................... 17 1.4.3 Military...................................................................................................................... 17 1.4.4 Homeland security...................................................................................................... 18 1.4.5 Public safety .............................................................................................................. 18 1.4.6 O&G drill support ....................................................................................................... 18 1.4.7 Inspection, repair, and maintenance............................................................................. 19 1.4.8 Construction (O&G as well as civil)............................................................................... 19 1.5 Conclusions....................................................................................................................................
1.1 The ROV
1.1.1 What is an ROV?
Currently, underwater vehicles fall into two basic categories (Figure 1.1): manned underwater vehi- cles and unmanned underwater vehicles (UUVs). The US Navy often uses the definition of UUV as synonymous with autonomous underwater vehicles (AUVs), although that definition is not a stan- dard across the industry.
power of the vehicle can be onboard (i.e., battery or engine powered), offboard (i.e., power deliv- ered through conductors within the tether), or a hybrid of both (e.g., onboard battery powered with a power recharge transmitted remotely through the tether). Simplistically, an ROV is a camera mounted in a waterproof enclosure, with thrusters for maneuvering, attached to a cable to the surface over which a video signal and telemetry are trans- mitted (Figure 1.2). Practically all of today’s vehicles use common industry standards for commer- cial off-the-shelf (COTS) components. As the ROV goes from its simplest shallow water form toward the more complex deep water work vehicles, the required degree of sophistication of its operators as well as the depth of its sup- port network climbs substantially in a similar fashion to that of aircraft or large surface vehicles. The modern ROV is a mature technology with established standards of operator qualifications, safe operations, and a proven history of getting work done in the “dull, dirty and dangerous” work environments of the world’s waters. The following sections will provide a better understanding of the scope of this definition. Subsequent chapters will provide in-depth discussions of the design of ROV systems along with operational considerations.
1.1.2 ROV size classifications
ROVs can be more specifically described as teleoperated free-swimming robotic unmanned (or “uninhabited” for the more modern term) underwater vehicles. These are used in a variety of appli- cations from diver support to heavy marine subsea construction. The market is substantially seg- mented into four broad categories based upon vehicle size and capabilities:
Control Console Controller
Submersible
Tether
Monitor
FIGURE 1.
Basic ROV system components.
surface with hand tending of the tether. The older/antiquated term for vehicles of this classification is “low-cost ROVs.”
FIGURE 1.
Examples of OCROVs (Note: shoes atop for scaling). (Courtesy SeaTrepid.)
FIGURE 1.
Example of MSROV. (Courtesy Forum Energy Technologies.)
worldwide population of WCROVs is hydraulic due to the power requirement and the inherent reli- ability of hydraulic systems over their electric counterparts within the seawater environment. OCROVs are generally called “flying eyeballs” as their main job is to function as a shallow water video platform. The MSROV has additional deepwater capabilities along with fiber optic telemetry for full gigabit sensor throughput. The WCROV possesses all of the attributes of both the OCROV and the MSROV along with high-powered hydraulic manipulators and tooling capabilities (Table 1.1). Table 1.2 depicts representative vehicle configurations and power/telemetry requirements. Configurations vary within each category from vehicle to vehicle, but these represent the general characteristics of vehicles within the specified size category. For specific vehicle parameters, please consult the vehicle manufacturer’s technical specifications.
1.1.3 Vehicle shape versus mission
The length to width (termed “aspect”) ratio of the vehicle directly affects its hydrodynamics. Long slender vehicles generally have lower drag characteristics at higher speeds but exhibit poor station- holding capabilities. Short vehicles have much better station-keeping capabilities along with higher maneuverability in all three axes of travel (x/y/z) but have much higher drag profiles as the speed ramps up. AUVs typically exhibit the classical torpedo shape with a high aspect ratio and minimal number of thrusters coupled with control fins for long-distance travel at higher speeds. The ROV is typically used in station-keeping (or slow speed observation) tasks for close inspection and/or sen- sor and tooling delivery. AUVs typically have a closed frame for uninterrupted fluid flow about the vehicle (for minimal drag at higher speeds) while ROVs typically have an open frame to allow for fluid flow through the frame due to a higher number of internally mounted thrusters.
Table 1.1 ROV Classifications Classification General Capability OCROV Flying eyeball with limited intervention MSROV Full gigabit data throughput with light intervention WCROV Full gigabit data throughput with heavy intervention
Table 1.2 Representative Vehicle Characteristics Size Category
Input Power
Vehicle Power
Telemetry Type
Depth Rating
Launch Method
TMS Thruster/ Tooling
Tooling Fluid Flow OCROV 110/ VAC 1Φ
Low-voltage DC
Copper only
1 / 2 300 m (1000 ft)
Hand deploy
No Electric/ electric
Electric only MSROV 440/ VAC 3Φ
Medium- voltage DC or AC
Copper or fiber
.1000 m (3000 ft)
Crane or A-frame
Optional Electric/ hydraulic
15 lpm (4 gpm)
WCROV 440/ VAC 3Φ
High-voltage AC
Fiber only .3000 m (10,000 ft.)
A-frame Yes Hydraulic/ hydraulic
70 lpm (18 gpm)
Within the ROV group, vehicles with a higher aspect ratio are used for longer travel distances (e.g., pipeline surveys or regional transects) while lower aspect ratio vehicles are used for close inspections or tasks requiring station-keeping capabilities.
1.1.4 ROV depth rating by classification
General man and machine capabilities for working within the marine environment fall within the depth limitations provided in Table 1.3. At the current state of technology for telepresence with mobile robotic systems, man (a diver) in the environment will be much more capable than a machine. This is due to the in situ situational awareness provided by man as well as the ultimate dexterity of the end effector (a hand for a man and a manipulator claw for the machine). But the costs and danger of placing man in the high- pressure work environment of the deep sea are considerable. Within the commercial, scientific, and governmental industries, more and more customers are looking for a robotic solution to the ever- increasing requirements for subsea sensing and intervention; their goal is to limit the cost and lia- bility exposure brought on from possibly harming “the man.” Look for vast future improvements in both the technology and demands for this category of robotics.
1.1.5 Size versus ability to deploy sensors/tooling
It is best to view any underwater vehicle as simply a “bus ride to the work site.” The purpose of the vehicle will always be the delivery of the sensor and/or tooling package to the work site in order to accomplish the mission. The question then becomes: “How large does the vehicle need to be in order to effectively accommodate the sensors and tooling package?” In general, any ROV can float any sensor or tooling package—all that is necessary is to place ample flotation aboard the vehicle to offset the in-water weight of the payload. The size of the vehicle then needs to vary to optimally accommodate the prime mover (thrusters), tooling, and sen- sors while still powering these items and thrusting/moving the package. Also, communication capa- bilities must match the sensor bandwidth requirements to ensure sufficient data throughput exists to transmit the telemetry to the operator station for logging sensor data and controlling the tooling package.
Table 1.3 Capabilities Versus Depth Category Depth Limitation Air diving 190 ft (60 m) Mixed gas diving 300 ft (100 m) Saturation diving 1000 ft (300 m) Atmospheric diving system 2300 ft (700 m) OCROV 1000 ft (300 m) MSROV .3000 ft ( .1000 m) WCROV .10,000 ft ( .3000 m)