
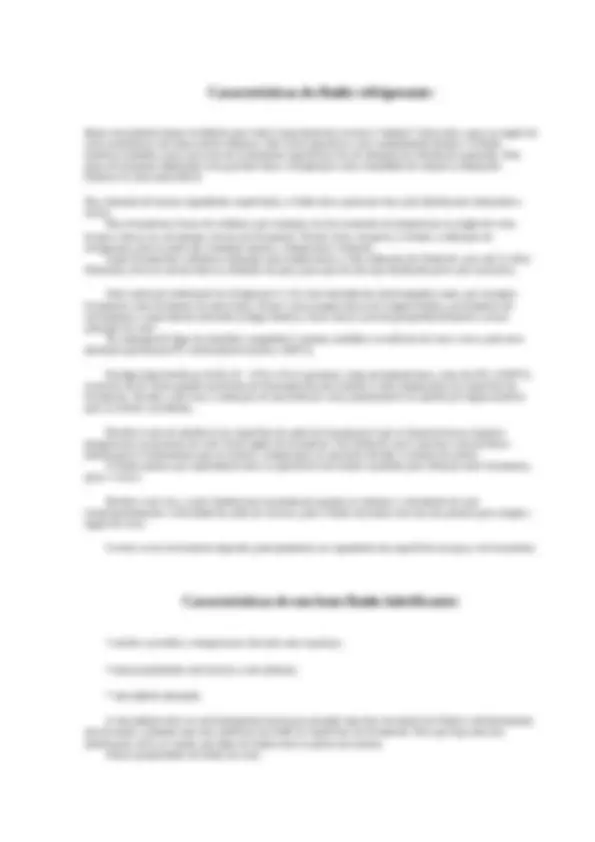
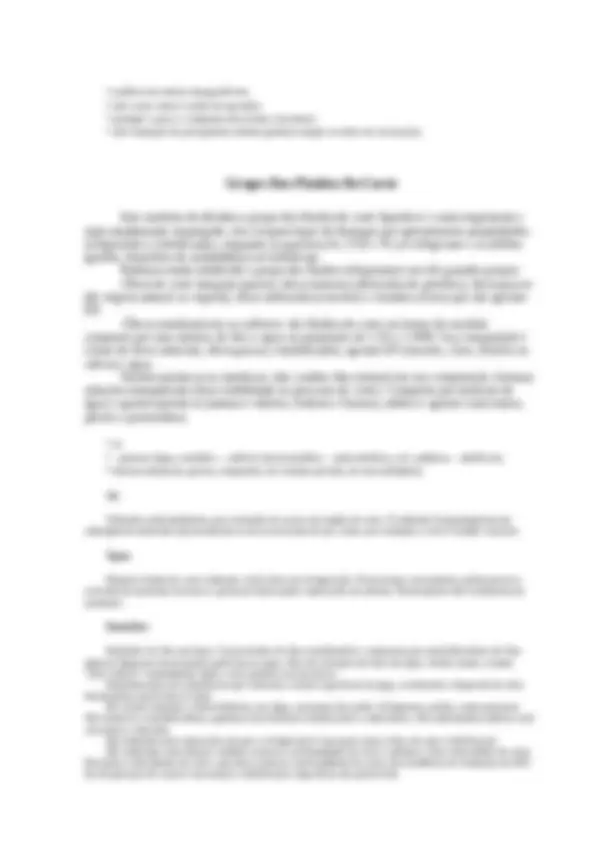
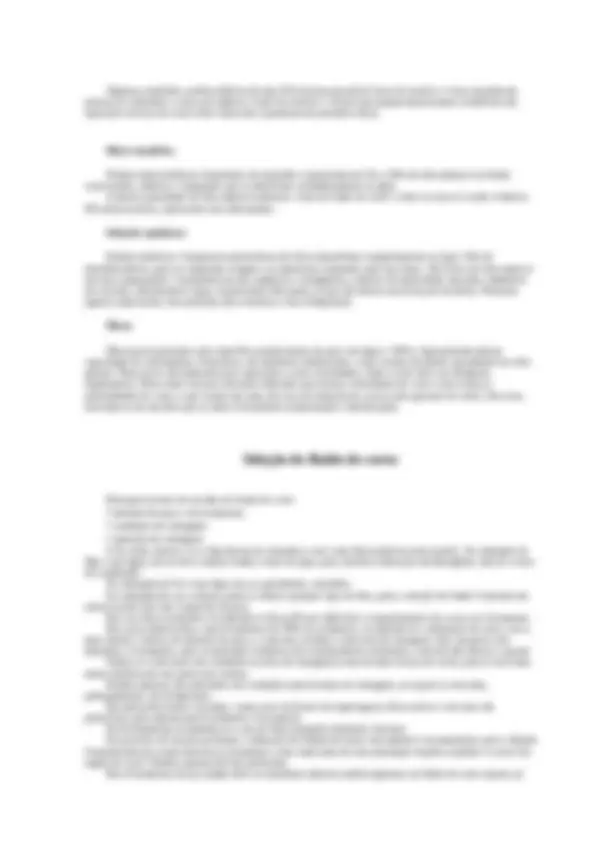
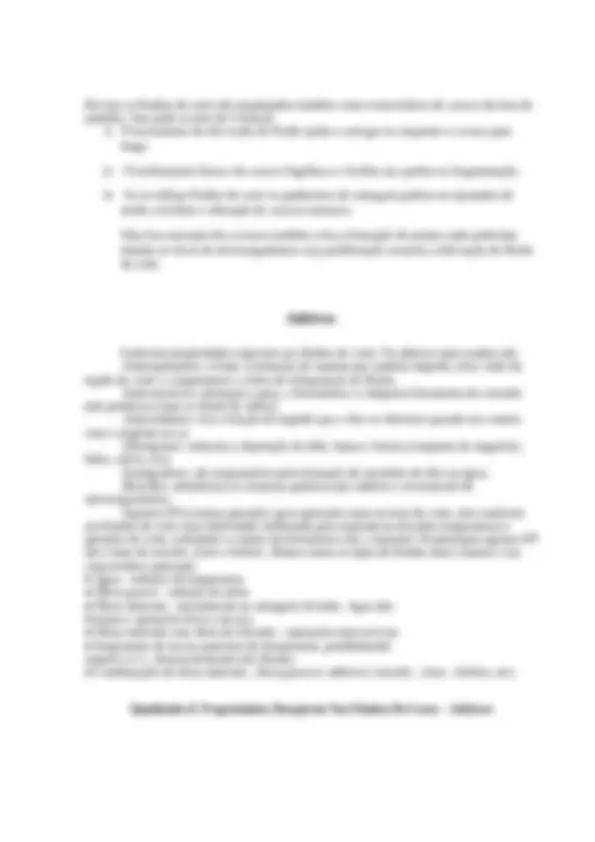
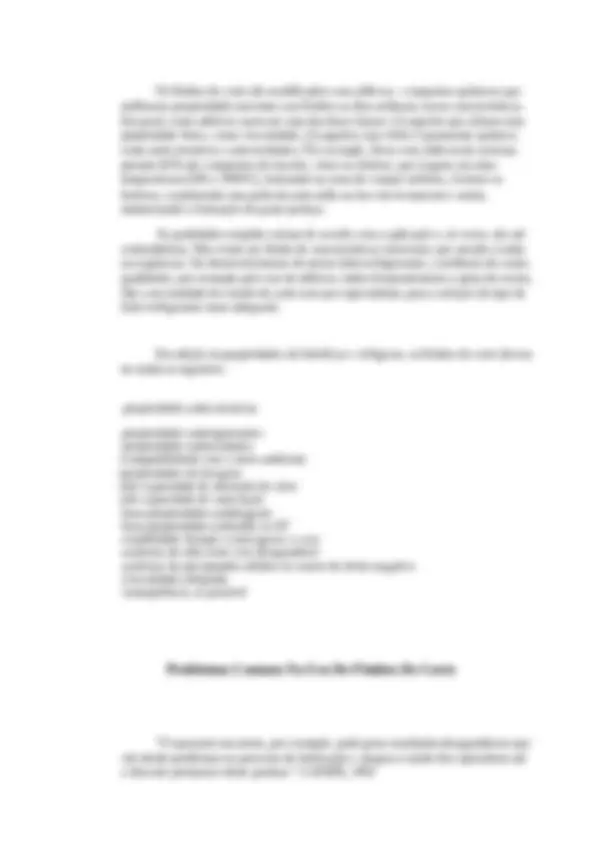
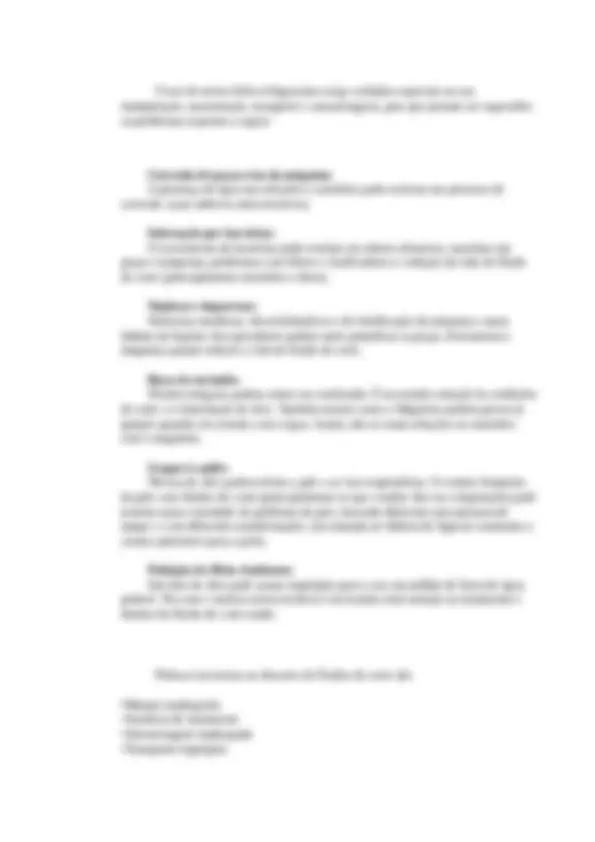
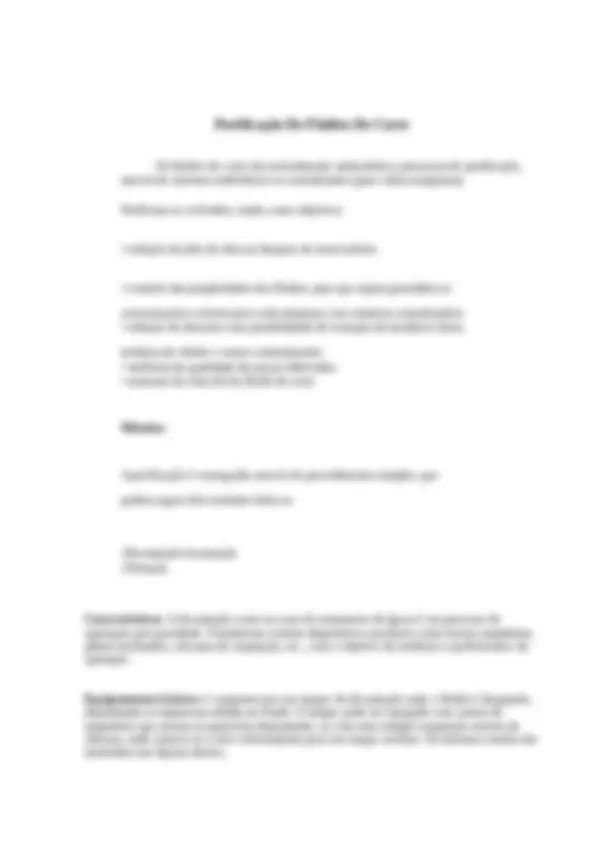
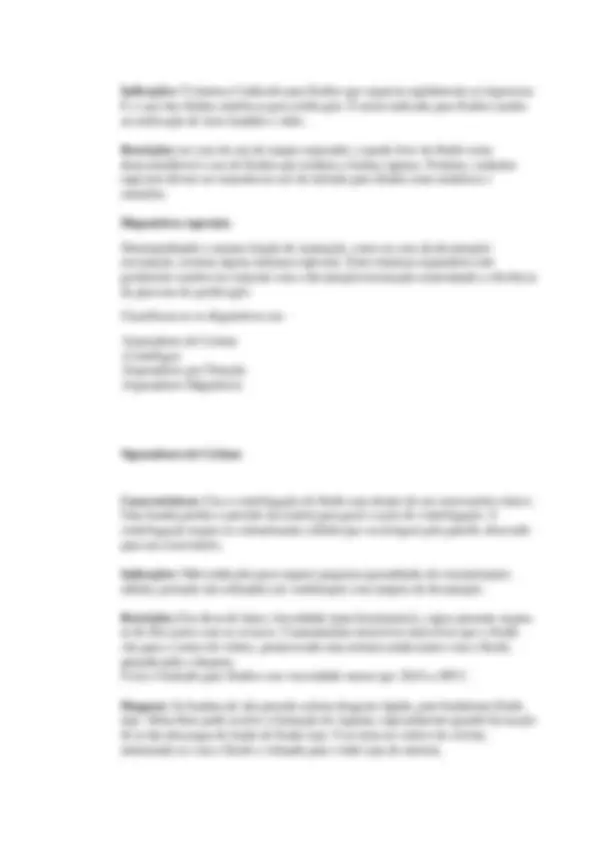
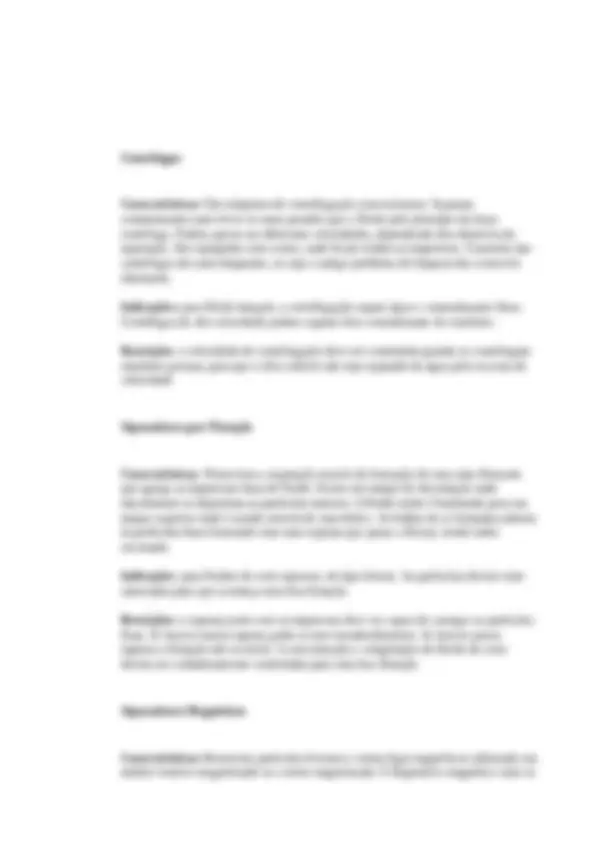
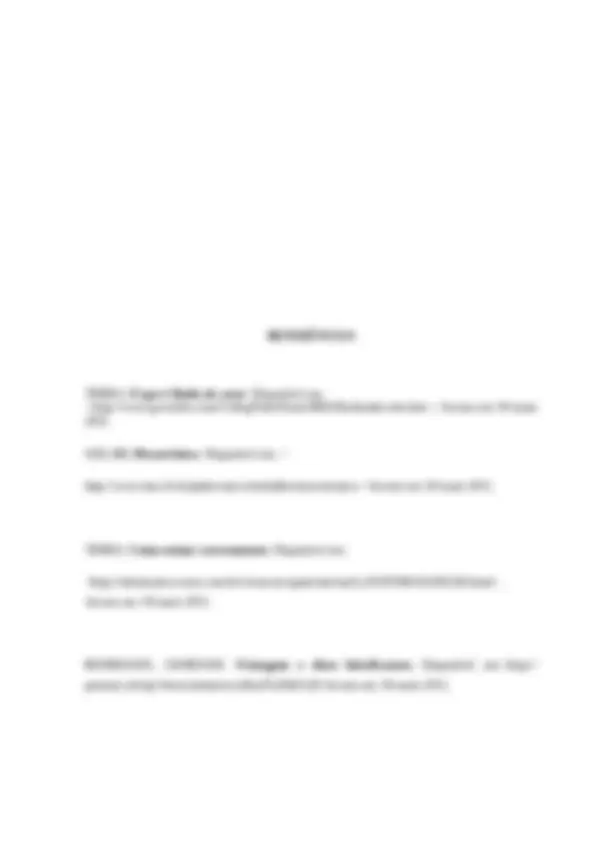
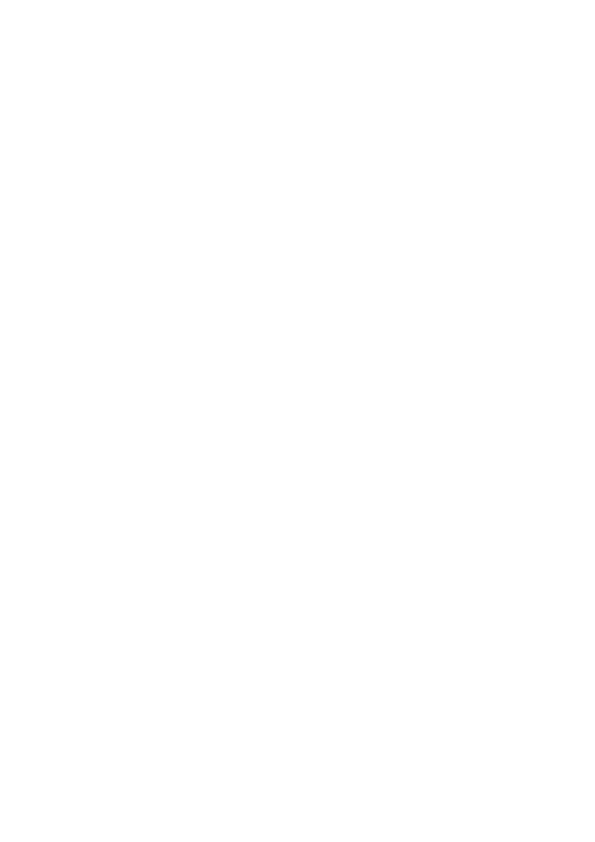
Estude fácil! Tem muito documento disponível na Docsity
Ganhe pontos ajudando outros esrudantes ou compre um plano Premium
Prepare-se para as provas
Estude fácil! Tem muito documento disponível na Docsity
Prepare-se para as provas com trabalhos de outros alunos como você, aqui na Docsity
Os melhores documentos à venda: Trabalhos de alunos formados
Prepare-se com as videoaulas e exercícios resolvidos criados a partir da grade da sua Universidade
Responda perguntas de provas passadas e avalie sua preparação.
Ganhe pontos para baixar
Ganhe pontos ajudando outros esrudantes ou compre um plano Premium
Comunidade
Peça ajuda à comunidade e tire suas dúvidas relacionadas ao estudo
Descubra as melhores universidades em seu país de acordo com os usuários da Docsity
Guias grátis
Baixe gratuitamente nossos guias de estudo, métodos para diminuir a ansiedade, dicas de TCC preparadas pelos professores da Docsity
trabalho sofre fluidos de corte
Tipologia: Trabalhos
1 / 19
Esta página não é visível na pré-visualização
Não perca as partes importantes!
Um fluido de corte é um material composto, na maioria das vezes líquida, usado na indústria com a função de refrigerar, lubrificar, proteger contra a oxidação e limpar a região da usinagem.
Após refrigerar a ferramenta e a peça, o fluido cai para a mesa onde é recolhido por canais e levado por meio de um tubo para o reservatório, assim a bomba aspira novamente o fluido para devolvê-lo sobre a ferramenta e a superfície do trabalho. O fluido pode ser sólido, líquido e gasoso e estão divididos em três grupos: óleos de corte integrais; óleos emulsionáveis ou solúveis e; fluido de corte químico. Os aditivos mais usados são os antioxidantes e os agentes EP. Os agentes EP são aditivos que reagem quimicamente com a superfície metálica e formam uma película que reduz o atrito. Alguns tipos de agentes EP são a matéria graxa, o enxofre, o cloro e o fósforo. F. W. Taylor foi um dos primeiros a provar o grande auxílio que os líquidos poderiam trazer no corte de metais. Em 1883, ele demonstrou que um jato de água aspergido na ferramenta, no cavaco e na superfície da peça tornava possível o aumento da velocidade de corte em 30% a 40%. Foi essa constatação, feita por Taylor e por outros pesquisadores, que impulsionou o estudo e o desenvolvimento de vários tipos de fluidos de corte ao longo dos anos e, principalmente, nas últimas décadas (Silliman, 1992; Machado & Diniz, 2000). Segundo Novaski & Dörr (1999), a utilização de uma quantidade cada vez menor de fluido na região de corte, mas de modo a não comprometer a usinagem, tem grande importância no cotidiano das indústrias
Os gastos com refrigeração representam, em média, 17% dos custos de manufatura, um valor expressivo, se comparado aos destinados à ferramenta, que apresenta, em média, de 2 a 4%, além das despesas de manutenção do sistema e separação do cavaco do fluido de corte para uma posterior refundição.
De acordo com Baradie (1996), nas indústrias, somente mais recentemente a correta seleção e aplicação dos fluidos de corte ganhou maior importância. Quando necessário no processo de retificação, se o fluido de corte for corretamente aplicado pode aumentar a produtividade e reduzir os custos, permitindo o uso de maiores velocidades de corte, altas taxas de remoção e grandes profundidades de corte. Além disso, uma efetiva aplicação possibilita aumentar a vida da ferramenta e a precisão dimensional e diminuir a rugosidade superficial da peça e a potência consumida.
Os fluidos de corte são parte integrante dos processos de fabricação de peças no contexto que reúne máquinas ferramentas, ferramentas de corte, produção de peças e fluidos de corte (Runge & Duarte, 1990).
Taylor (1890): 1ª utilização do fluido de corte (água + soda). Água: alto poder refrigerante, porém causa oxidação na peça. Com o tempo tem-se o objetivo de restringir ao máximo o uso de refrigerante:
Para minimizar estes problemas:
Durante o corte, se desenvolve grande quantidade de calor, devido a energia necessária para deformação do cavaco e a energia devido ao atrito ferramenta-peça, cavaco-ferramenta. Reduz-se este calor através da lubrificação (diminuição do atrito) e/ ou da refrigeração, a fim de minimizar-se o desgaste da ferramenta, a dilatação térmica da peça e o dano térmico à superfície da peça (obtenção de tolerâncias apertadas e formas). Reduzindo-se o atrito reduzem-se também os esforços de corte. Pode-se também reduzir a formação da APC e a soldagem do cavaco na ferramenta. Formas de redução do atrito: revestimentos de ferramentas, materiais de peça com usinabilidade melhorada e utilização de fluidos de corte com capacidade lubrificante. O calor continua a ser gerado independentemente das medidas tomadas. A lubrificação é facilitada em baixas velocidades de corte, já que, nestas condições, a penetração do fluido nas interfaces cavaco-ferramenta e peça-ferramenta é facilitada. O fluido é importante também, para a expulsão do cavaco da região de corte e para proteção contra corrosão.
O calor excessivo prejudica a qualidade do trabalho por várias razões: -Diminui a vida útil da ferramenta; -Aumenta a oxidação da superfície da peça e da ferramenta; -Aumenta a temperatura da peça, provocando dilatação, erros de medidas e deformações. Para resolver estes problemas surgiram fluidos de corte, que são agentes de melhoria na usinagem. A busca por valores maiores de VC sempre foi almejado em virtude de uma maior produção de peças, e isso foi possível devido ao surgimento de novos materiais de corte (metal duro, cerâmicas, ultra-duros “PCB” e “PCD”) capazes de usinar os materiais com altíssimas VC, em contrapartida grandes valores de temperaturas foram geradas na região de corte devido a um grande atrito entre a peça e a ferramenta. Os fluidos de corte podem se sólidos, gases e , na maioria das vezes, líquidos. Freqüentemente são chamados de lubrificantes ou refrigerantes em virtude das suas principais funções na usinagem.: -Aumento da vida da ferramenta pela lubrificação e refrigeração (diminuição da temperatura); -Redução das forças de corte devido a lubrificação, portanto redução de potência; -Melhora do acabamento superficial; -Fácil remoção do cavaco da zona de corte; -Menor distorção da peça pela ação da ferramenta (controle dimensional da peça).
Sem sombras de dúvidas o grupo dos fluidos de corte líquidos é o mais importante e mais amplamente empregado, eles ocupam lugar de destaque por apresentarem propriedades refrigerantes e lubrificantes, enquanto os gasosos (Ar, CO2 e N ) só refrigeram e os sólidos (grafite, bissulfeto de mobilidênio) só lubrificam. Podemos ainda subdividir o grupo dos fluidos refrigerantes em três grandes grupos: -Óleos de corte integrais (puros): óleos minerais (derivados de petróleo), óleos graxos (de origem animal ou vegetal), óleos sulfurados (enxofre) e clorados (cloro) que são agentes EP; -Óleos emulsionáveis ou solúveis: são fluidos de corte em forma de emulsão composto por uma mistura de óleo e água na proporção de 1:10 a 1:1000. Sua composição é à base de óleos minerais, óleos graxos, emulsificados, agentes EP (enxofre, cloro, fósforo ou cálcio) e água. Fluidos químicos ou sintéticos: não contêm óleo mineral em sua composição, formam soluções transparentes (boa visibilidade no processo de corte). Composto por misturas de água e agentes químicos (aminas e nitritos, fosfatos e boratos, sabões e agentes umectantes, glicóis e germicidas).
Ar:
Utilizada, principalmente, para remoção de cavaco da região de corte. É utilizado frequentemente em usinagem de materiais que produzem cavacos em forma de pó, como, por exemplo, o ferro fundido cinzento.
Água:
Primeiro fluido de corte utilizado. Ação única de refrigeração. Possui baixa viscosidade, porém provoca corrosão de materiais ferrosos e apresenta baixo poder umectante nos metais. Praticamente não é utilizada em produção.
Emulsões:
Emulsões de óleo em água. Concentrados de óleo emulsionável, compostos por emulsificadores de óleo mineral dispersos em pequenas gotículas na água. Não são soluções de óleo em água. Sendo assim, o nome “óleo solúvel” normalmente dado a este produto está incorreto. Emulsificantes são substâncias que reduzem a tensão superficial da água, facilitando a dispersão do óleo em pequenas partículas na água. Por serem formadas, essencialmente, por água, possuem alto poder refrigerante, porém, como possuem óleo mineral e emulsificadores, ganham características lubrificantes e umectantes. São adicionados aditivos anti- corrosivos e biocidas. São indicadas para operações em que a refrigeração é um ponto mais crítico do que a lubrificação. São utilizadas com baixos e médios avanços e profundidade de corte e médias e altas velocidades de corte. Em baixas velocidades de corte com altos avanços e profundidade de corte (alta tendência de formação da APC de alta geração de calor) é necessária a lubrificação, logo óleos são preferíveis.
Algumas emulsões contêm aditivos do tipo EP (extrema pressão) à base de enxofre e cloro (atualmente procura-se substituir o cloro por aditivos à base de enxofre e cálcio) que proporcionam maior resistência em operações severas de corte (estes óleos não vaporizam em pressões altas).
Micro emulsões:
Fluidos semi-sintéticos formadores de emulsões. Apresentam de 5% a 50% de óleo mineral no fluido concentrado, aditivos e compostos que se dissolvem verdadeiramente na água. A menor quantidade de óleo mineral aumenta a vida do fluido de corte e reduz os riscos à saúde. Aditivos EP, anticorrosivos, umectantes são adicionados.
Soluções químicas:
Fluidos sintéticos. Compostos monofásicos de óleos dissolvidos completamente na água. Não há emulsificadores, pois os compostos reagem e se misturam, formando uma fase única. São livres de óleo mineral em suas composições. Consistem em sais orgânicos e inorgânicos, aditivos de lubricidade, biocidas, inibidores de corrosão, adicionados à água. Apresentam vida maior, já que são menos atacáveis por bactérias. Possuem agentes umectantes, boa proteção anti-corrosiva e boa refrigeração.
Óleos:
Óleos puros possuem calor específico muito menor do que o da água (~50%), logo possuem menor capacidade de resfriamento. Entretanto, são melhores lubrificantes, o que resulta em menor quantidade de calor gerado. Óleos leves são indicados para operações a altas velocidades, onde o calor deve ser dissipado rapidamente. Óleos mais viscosos são mais indicados para baixas velocidades de corte e alto avanço e profundidade de corte, o que resulta em uma alta taxa de remoção de cavaco (alta geração de calor). Para isto, necessita-se de um óleo que se adira à ferramenta (aumentando a lubrificação).
Principais fatores de escolha do fluido de corte:
Refrigerar a região de corte.
A refrigeração desempenha um papel fundamental na usinagem. Uma das principais funções dos fluidos de corte é refrigerar, ou seja, remover o calor gerado durante a operação. Isso ajuda a prolongar a vida útil das ferramentas e a garantir a precisão dimensional das peças pela redução dos gradientes térmicos.
Lubrificar as superfícies em atrito.
Nos processos de usinagem, a lubrificação nas interfaces peça-ferramenta-cavaco é difícil e complexa, em virtude das elevadas pressões de contato nessas interfaces. Outro agravante é a dificuldade de levar esse lubrificante até a posição desejada. A forma como o fluido penetra na região de contato cavaco-ferramenta é uma questão ainda em discução entre pesquisadores. A eficiência do lubrificante vai depender das características e da sua habilidade em penetrar na região entre o cavaco e a ferramenta, formando um filme com resistência ao cisalhamento menor que a resistência do material na interface. Tanto a superfície do cavaco quanto a da ferramenta não são perfeitamente lisas. Elas são rugosas, ou seja, apresentam minúsculas saliências, asperezas em forma de picos e vales da ordem de micrômetros. Os picos mais salientes atritam-se, desgastando a ferramenta, gerando calor e uma força de atrito. Com a progressão do desgaste, pequenas partículas soldam-se no gume da ferramenta, formando o gume postiço. Para reduzir esse atrito, o fluido de corte penetra na interface rugosa por capilaridade.(Runge, P. 1990) Como consequência, reduz-se uma parcela da geração de calor. Também reduzem-se o consumo de energia, a força necessária ao corte e praticamente elimina-se o gume postiço.
Arrastar o cavaco da área de corte.
Em alguns processos de usinagem é muito importante considerar o destino do cavaco após a sua formação. O cavaco formado deve ser retirado da área de trabalho para não riscar ou comprometer o acabamento da peça, danificar a ferramenta ou impedir a própria usinagem. Na furação profunda, por exemplo, o cavaco formado no fundo do furo tende a se acumular excessivamente, dificultando o corte e a formação de mais cavaco. Até mesmo no torneamento externo, cavacos em forma de fitas longas podem se enroscar na peça e na ferramenta e atrapalhar o trabalho.
Por isso os fluidos de corte são empregados também como removedores de cavaco da área de trabalho. Isso pode ocorrer de 3 formas:
O escoamento de alta vazão do fluido ajuda a carregar ou empurrar o cavaco para longe.
O resfriamento brusco do cavaco fragiliza-o e facilita sua quebra ou fragmentação.
Ao se utilizar fluidos de corte os parâmetros de usinagem podem ser ajustados de modo a facilitar a obtenção de cavacos menores.
Uma boa remoção dos cavacos também evita a formação de pontos onde poderiam instalar-se focos de microorganismos cuja proliferação causaria a infectação do fluido de corte.
Conferem propriedades especiais aos fluidos de corte. Os aditivos mais usados são: -Antiespumantes: evitam a formação de espuma que poderia impedir a boa visão da região de corte e comprometer o efeito de refrigeração do fluido; -Anticorrosivos: protegem a peça, a ferramenta e a máquina-ferramenta da corrosão (são produtos à base se nitrito de sódio); -Antioxidantes: tem a função de impedir que o óleo se deteriore quando em contato com o oxigênio no ar; -Detergentes: reduzem a deposição de iôdo, lamas e borras (composto de magnésio, bário, cálcio, etc); -Emulgadores: são responsáveis pela formação de emulsões de óleo na água; -Biocidas: substâncias ou misturas químicas que inibem o crescimento de microorganismos; -Agentes EP (extrema pressão): para operações mais severas de corte, eles conferem aos fluidos de corte uma lubricidade melhorada para suportarem elevadas temperaturas e pressões de corte, reduzindo o contato da ferramenta com o material. Os principais agentes EP são à base de enxofre, cloro e fósforo. Abaixo temos os tipos de fluidos mais comuns e sua característica principal; ● Água - redução da temperatura ● Óleos graxos - redução do atrito ● Óleos minerais - inicialmente na usinagem de latão, ligas não- ferrosas e operações leves com aço ● Óleos minerais com óleos de toicinho - operações mais severas ● Surgimento de novos materiais de ferramentas, possibilitando maiores vc‘s - desenvolvimento dos fluidos ● Combinações de óleos minerais , óleos graxos e aditivos ( enxofre , cloro , fósforo, etc)
Qualidades E Propriedades Desejáveis Nos Fluidos De Corte – Aditivos
O uso de meios lubri-refrigerantes exige cuidados especiais na sua
manipulação, manutenção, transporte e armazenagem, para que possam ser superados
os problemas expostos a seguir.
Corrosão de peças e/ou da máquina: A presença de água nas soluções e emulsões pode acelerar um processo de
corrosão. (usar aditivos anticorrosivos)
Infectação por bactérias: O crescimento de bactérias pode resultar em odores ofensivos, manchas nas peças e máquinas, problemas com filtros e clarificadores e redução da vida do fluido
de corte (principalmente emulsões e óleos).
Sujeiras e impurezas: Partículas metálicas, óleos hidráulicos e de lubrificação da máquina e maus
hábitos de higiene dos operadores podem tanto prejudicar as peças, ferramentas e máquinas quanto reduzir a vida do fluido de corte.
Risco de incêndio: Fluidos integrais podem entrar em combustão. É necessário atenção às condições
de corte e à formulação do óleo. Também metais como o Magnésio podem provocar
ignição quando em contato com a água. Assim, não se usam soluções ou emulsões com o magnésio.
Ataque à saúde: Névoas de óleo podem irritar a pele e as vias respiratórias. O contato freqüente
da pele com fluidos de corte (principalmente os que contém óleo na composição) pode
resultar numa variedade de problems de pele, havendo diferentes mecanismos de ataque e com diferentes manifestações. (recomenda-se hábitos de higiene constantes e
cremes protetores para a pele).
Poluição do Meio-Ambiente: Um litro de óleo pode tornar impróprio para o uso um milhão de litros de água potável. Por esse e muitos outros motivos é necessária total atenção ao tratamento e
destino do fluido de corte usado.
Práticas incorretas no descarte de fluidos de corte são:
•Manejo inadequado •Ausência de tratamento
•Armazenagem inadequada
•Transporte impróprio
•Entrega a receptores não autorizados •Disposição de resíduos em local não autorizado.
Escolher o fluido de corte ideal para cada situação é tão complexo quanto
escolher o material e o tipo da ferramenta. Para isso, é fundamental conhecer amplamente o processo de produção. O engenheiro deve ter claro qual é o objetivo a
ser alcançado com o uso do fluido: maior produção, mais vida de ferramenta ou
precisão dimensional para citar alguns.
São muitos os fatores que influenciam a escolha de um fluido de corte. Aqui
são citados os mais comuns.
-Processo de Usinagem -Máquina-Ferramenta utilizada
-Produção (diversidade de produtos e matérias)
-Análise Econômica -Operadores e Meio Ambiente
-Recomendações dos Fabricantes
Variáveis de Corte
•Como regra geral: usinabilidade baixa > baixa v (^) c > Lubrificação > Fluidos integrais. usinabilidade alta > alta vc > Refrigeração > Soluções ou Emulsções.
Material da Peça
•Magnésio: Nunca usar fluido à base de água > risco de ignição.
•Ferro Fundido: Cinzento e o Maleável > geralmente usinagem a seco. Esferoidal > Emulsão.
•Alumínio:
Os fluidos de corte são normalmente submetidos a processos de purificação, através de sistemas individuais ou centralizados (para várias máquinas).
Purificam-se os fluidos, tendo como objetivos:
concentrações corretas para cada máquina ( nos sistemas centralizados)
resíduos de rebolo e outros contaminantes
Métodos
A purificação é conseguida através de procedimentos simples, que
podem seguir dois métodos básicos:
-Decantação/escumação. -Filtração.
Características : A decantação como no caso do tratamento de águas é um processo de separação por gravidade. Usualmente existem dispositivos auxiliares como barras raspadoras, planos inclinados, chicanas de separação, etc., com o objetivo de melhorar a performance da operação.
Equipamentos básicos: é composto por um tanque de decantação onde o fluido é despejado, depositando as impurezas sólidas no fundo. O tanque pode ser equipado com esteira de raspadores que arrasta as partículas depositadas, ou com uma simples separação através de chicana, onde remove-se o óleo sobrenadante para um tanque auxiliar. Os sistemas citados são mostrados nas figuras abaixo.
Indicações: O sistema é indicado para fluidos que separem rapidamente as impurezas.
É o caso dos fluidos sintéticos para retificação. É muito indicada para fluidos usados
na retificação de ferro fundido e vidro.
Restrições: no caso do uso do tanque separador, a queda livre do fluido torna
desaconselhável o uso de fluidos que tendem a formar espuma. Portanto, cuidados especiais devem ser tomados no uso do método para fluidos semi-sintéticos e
emulsões.
Dispositivos especiais.
Desempenhando a mesma função de separação, como no caso da decantação/ escumação, existem alguns sistemas especiais. Estes sistemas separadores são
geralmente usados em conjunto com a decantação/escumação aumentando a eficiência
do processo de purificação.
Classificam-se os dispositivos em :
-Separadores de Ciclone
-Centrífugas -Separadores por Flotação
-Separadores Magnéticos
Separadores de Ciclone
Características: Usa a centrifugação do fluido sujo dentro de um reservatório cônico. Uma bomba produz a pressão necessária para gerar a ação de centrifugação. A
centrifugação separa os contaminantes sólidos que escorregam pela parede, descendo
para um reservatório.
Indicações: Mais indicados para separar pequenas quantidades de contaminantes
sólidos, portanto são utilizados em combinação com tanques de decantação.
Restrições: Em óleos de baixa viscosidade (para brunimento), a água presente separa- se do óleo junto com os cavacos. Contaminantes imiscíveis mais leves que o fluido
vão para o centro do vórtice, promovendo uma mistura ainda maior com o fluido,
prejudicando a limpeza. O uso é limitado para fluidos com viscosidade menor que 20cSt a 400 C.
Desgaste: As bombas de alta pressão sofrem desgaste rápido, pois bombeiam fluido sujo. Além disto pode ocorrer a formação de espuma, especialmente quando há sucção
de ar das descargas de fundo de fluido sujo. O ar entra no vórtice do ciclone,
misturando-se com o fluido e voltando para o lado sujo do sistema.
partículas metálicas, levando-as para fora da área do fluxo do fluido de corte. Em alguns equipamentos existem acessórios raspadores que fazem a remoção final das partículas.
Indicações: para fluidos de corte aquosos e integrais de baixa viscosidade. No caso de tambores, o entrelaçamento das partículas de impurezas magnetizadas formam uma rede que carrega também partículas não metálicas, favorecendo a limpeza.
Restrições: tem limitações de tamanho e capacidade de fluxo de fluido, portanto são adequados para uso em uma ou duas máquinas.
Não existe um fluido universal, a escolha do fluido com determinada composição depende do material a ser usinado, do tipo de operação e da ferramenta usada. Os fluidos de corte solúveis e os sintéticos são indicados quando a refrigeração for mais importante; Os óleos minerais e graxos usados juntos ou separados, puros ou contendo aditivos especiais, são usados quando a lubrificação for o fator mais determinante..
O uso correto dos fluidos de corte nos processos de usinagem pode trazer muitos benefícios , observados na qualidade e na produtividade. Por outro lado, se não forem manipulados e tratados corretamente, eles podem ser nocivos a saúde e ao meio ambiente. Assim, a escolha do fluido de corte influi diretamente na qualidade do acabamento superficial das peças, na produtividade, nos custos operacionais e também na saúde dos operadores e no meio-ambiente. Devemos tomar cuida com os seguintes ricos; ● Grande parte dos fluidos possui componentes que podem causar, além do impacto ambiental, doenças ao ser humano. ● Contato do fluido com o operário pode ser direto ou através de vapores, névoa ou subprodutos formados durante a usinagem. ● Doenças causadas pela ação direta com o fluído de corte
Concluímos que os fluidos de corte se tornaram uma ferramenta nos processos de usinagem, eles ajudam em diversas formas; No resfriamento das peças, na lubrificação, na remoção de cavaco etc. Percebemos também que devemos tomar cuidados pois alem de poder prejudicar a saúde do ser humano o fluido de corte pode prejudicar a natureza. Mais sem duvida os fluidos ajudam e muito nos processos de fabricação foi uma boa idéia quando começaram a usar a água como fluido, Hoje temos diversos tipos e para varias situações. Concluímos com isso que os fluidos é uma ferramenta que ainda será usada por um longo tempo para ajudar nos processos de usinagem.