
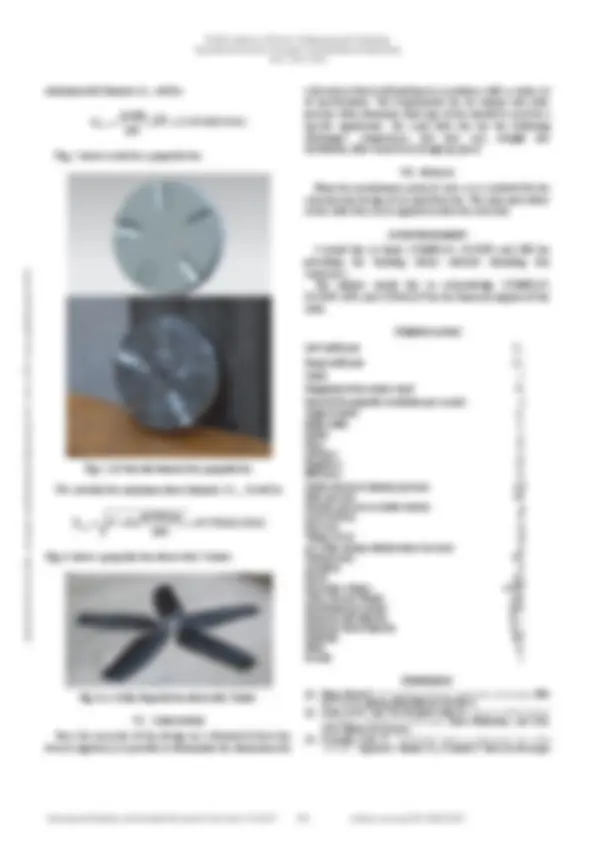
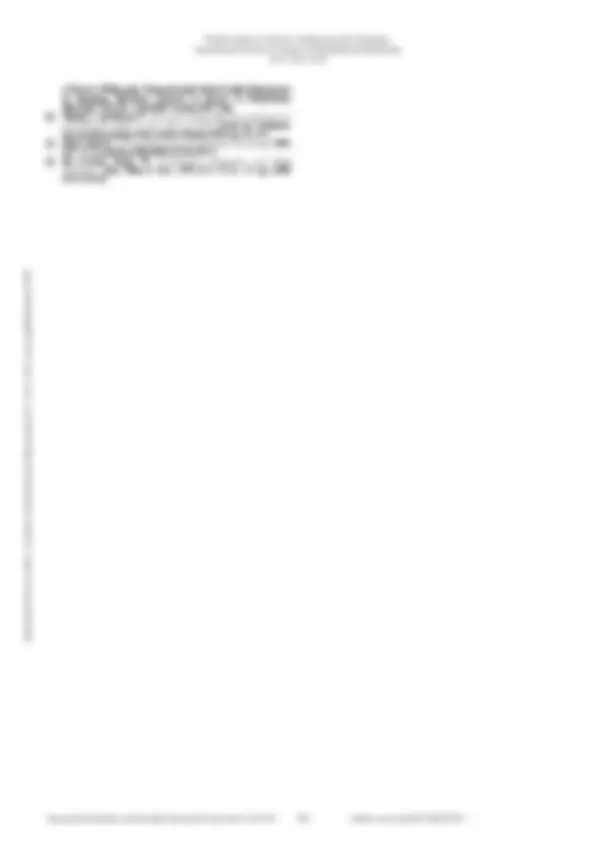
Estude fácil! Tem muito documento disponível na Docsity
Ganhe pontos ajudando outros esrudantes ou compre um plano Premium
Prepare-se para as provas
Estude fácil! Tem muito documento disponível na Docsity
Prepare-se para as provas com trabalhos de outros alunos como você, aqui na Docsity
Os melhores documentos à venda: Trabalhos de alunos formados
Prepare-se com as videoaulas e exercícios resolvidos criados a partir da grade da sua Universidade
Responda perguntas de provas passadas e avalie sua preparação.
Ganhe pontos para baixar
Ganhe pontos ajudando outros esrudantes ou compre um plano Premium
Comunidade
Peça ajuda à comunidade e tire suas dúvidas relacionadas ao estudo
Descubra as melhores universidades em seu país de acordo com os usuários da Docsity
Guias grátis
Baixe gratuitamente nossos guias de estudo, métodos para diminuir a ansiedade, dicas de TCC preparadas pelos professores da Docsity
turbomaquinaria special technical data measures
Tipologia: Resumos
1 / 4
Esta página não é visível na pré-visualização
Não perca as partes importantes!
Abstract — This work presents a methodology for the selection and design of propeller oriented to the experimental verification of theoretical results. The problem of propeller selection and design usually present itself in the following manner: a certain air volume and static pressure are required for a certain system. Once the necessity of fan design on a theoretical basis has been recognized, it is possible to determinate the dimensions for a fan unit so that it will perform in accordance with a certain set of specifications. The same procedures in this work then can be applied in other propeller selection.
Keywords — airfoil, axial flow, blade, fan, hub, mathematical algorithm, propeller design, simulation, wheel.
I. INTRODUCTION HE term axial flow fan indicates that the air flows through the fan in an approximately axial direction. On the inlet side, as the flow approaches the fan blades, the direction of the flow is axial, in other words, parallel to the axis of rotation, provided there are no inlet vanes or other restrictions ahead of the fan wheel. The fan blade then deflects the airflow, as show in the fig. 1:
Fig. 1 Airfoil as used in an axial flow fan blade [1]
A propeller is a mechanism designed to produce a tractive force or push, when submerged in a fluid medium. The
D. Almazo is an student of the Mechanical Engineering Department of the SEPI ESIME Zacatenco of IPN, Mexico City, Mexico (e-mail: diegomoisesal@hotmail.com). C. Rodríguez is a researcher with the Mechanical Engineering Department of the UANL, Monterrey City, Mexico (e-mail: crodrigue1@hotmail.com). M. Toledo is a researcher with the Mechanical Engineering Department of the SEPI ESIME Zacatenco of IPN, Mexico City, Mexico (e-mail: mtv49@yahoo.com).
propellers are aerodynamic elements that are composed of a hub or central core and a number of blades. The operating principle of axial-flow fans is simply deflection of airflow [2]. Past the blade, therefore, the pattern of the deflected airflow is of helical shape, like a spiral staircase. This is true for all three types of axial-flow fans: propeller fans, tubeaxial fans, and vaneaxial fans. Accordingly, the design procedures and the design calculations are similar for all three types. The helical pattern of the airflow past the blade of an axial flow fan the air velocity the can be resolved into two components: an axial velocity a tangential velocity. The axial velocity is the useful component. It moves the air to the location where we need it.
II. AIRFOIL An airfoil is a streamline shape. Its main application is as the cross section of an airplane wing. Another application is as the cross section of a fan blade. There are symmetric and asymmetric airfoils. The airfoils used in fan blade are asymmetric. Fig. 2 shows an asymmetric airfoil that has been developed by the National Advisory Committee for aeronautics (NACA); it is the NACA airfoil no.6512.
Fig. 2 NACA 6512 airfoil obtained from Matlab
As an airfoil moves through the air, it normally produces positive pressure on the lower surface of the airfoil and negative pressure or suction on the upper surface [3]. The suction pressure on the top surface are about twice as large as the positive pressures on the lower surface, but all these positive and negative pressures push and pull in approximately the same direction and reinforce each other. The combination of these positive and negative pressures results in a force F. This force F can be resolved into two components: a lift force L , perpendicular to the relative air velocity; and a drag force D , parallel to the relative air velocity. The lift force L is the useful component.
International Journal of Aerospace and Mechanical Engineering Vol:7, No:5, 2013
International Science Index, Aerospace and Mechanical Engineering Vol:7, No:5, 2013 waset.org/Publication/
For good efficiency, the airflow of an axial flow fan should be evenly distributed over the working face of the fan wheel. The axial air velocity should be the same from hub to tip. The velocity of the rotating blade is far from evenly distributed: it is low near the centre and increases toward the tip. This gradient should be compensated by a twist in the blade, resulting in larger blade angles near the center and smaller blade angles toward the tip. Fig. 3 shows an asymmetric airfoil as the cross section of a fan blade.
Fig. 3 An asymmetric NACA 6512 airfoil as the cross section of a fan blade
IV. NUMBER OF BLADES Turbulence and noise are mostly produced by the edges, both leading and trailing edges and not by the blade surface [4]. Therefore, fewer and wider blades will result in a better fan efficiency and a lower noise level. But if the number of blades becomes too small and the blade width too large, the fan cub becomes axially too wide and thus heavy, bulky, expensive, and hard to balance. Aerodynamically, the optimal number of blades would be one very wide blade, draped around the entry hub, but it would be an impractical and costly fan wheel. As a compromise between efficiency and cost, five to twelve blades are good practical solution [5]. Fig. 4 shows a propeller fan.
Fig. 4 A 1.618m propeller fan wheel
As far as the point of design is concerned, the designer has a certain amount of freedom in selecting the blade width at each radius can be compensated by corresponding variations in the lift coefficient CL [6].of the profile used in that section.
V. THE DIMENSIONS FOR AN AXIAL FLOW FAN Let us consider a duct area A = 1. 392 m^2 .The requirements call for ms
3 60 (127133cfm) at a static pressure of 495 Pascal (2inWC) to be produced by an axial fan at 2000rpm from an 84.438Kw motor: We can calculate the outlet velocity OV or q as :
2 2
OV = q = ρ V
where: OV=q = dynamic pressure or outlet velocity ρ= at 2240m density altitude above Sea level V = local velocity So
Q = AV
s
s m
m
m
2
3 = =
where: Q =Volume of air A = duct area V = local velocity The outlet velocity OV will be:
OV q ρ V
(0.982 )( 43. 103 ms^ ) 912 Pascal ( 3. 661 inWC ) 2
m
Kg 3 =
The total pressure will be:
TP = SP + VP = 495 + 912 = 1407 Pascal ( 5. 661 inWC )
The air power will be:
P=Air Volume x Total Pressure P ( 60 ms^ )( 1407 Pa ) 84. 438 Kw
3 = =
with an 84.438Kw motor this fan would have to have an 85 percent mechanical efficiency, which is more than can be expected. This means that an 84.438Kw motor would be overloaded. A 100.711Kw motor will be needed in order to get (^) s 60 m^3 at a static pressure of 495 Pascal. Let us calculate the minimum hub diameter dmin and the minimum wheel diameter Dmin for these requirements. The
0.1^ 0.
0.3 0.
0.5 0.
0.7 0.
0.9^1
-0.2-0. -0.1-0. (^0) -0.
-0. -0.
0
X
Z
International Journal of Aerospace and Mechanical Engineering Vol:7, No:5, 2013
International Science Index, Aerospace and Mechanical Engineering Vol:7, No:5, 2013 waset.org/Publication/
of Doctor of Philosophy, Università degli Studi di Cagliari Dipartimento di Ingegneria Meccanica Dottorato di Ricerca in Progettazione Meccanica XX Ciclo - Ing-Ind/09. January 2008, Italy. [4] Winkler J. and Moreau S., LES of the trailing-edge flow and noise of a NACA6512-63 airfoil at zero angle of attack. Center for Turbulence Research Proceedings of the Summer Program 2008. pp. 331–341. [5] Bleier, Frank P., Fan handbook selection, application, and design , 1998. N.Y., U.S.A. McGraw Hill ISBN 0-07-005933-0. [6] Mc Cormick, Barnes W., Aerodinamics, Aeronautics, and Flight Mechanics , Johns Wiley & Sons, 1979, N.Y. U.S.A. 652 pp. ISBN
International Journal of Aerospace and Mechanical Engineering Vol:7, No:5, 2013
International Science Index, Aerospace and Mechanical Engineering Vol:7, No:5, 2013 waset.org/Publication/