
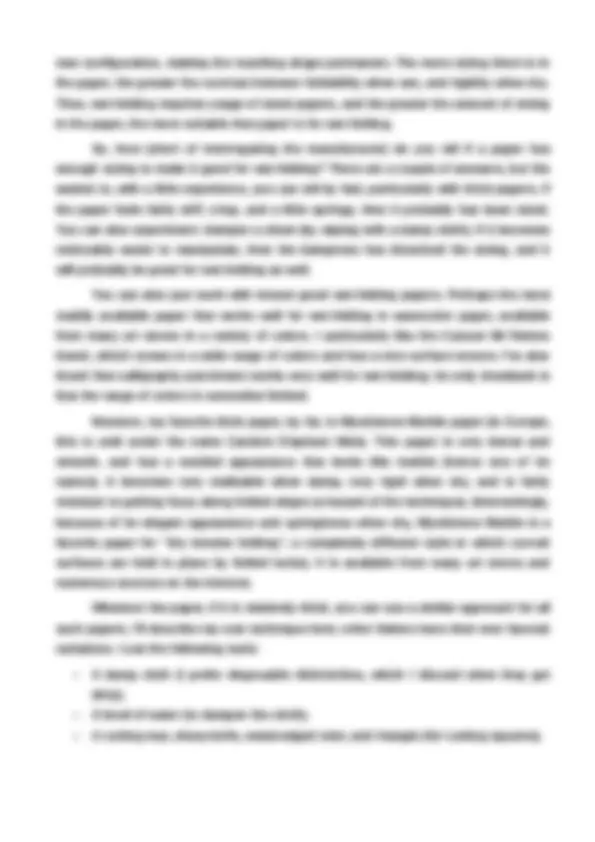
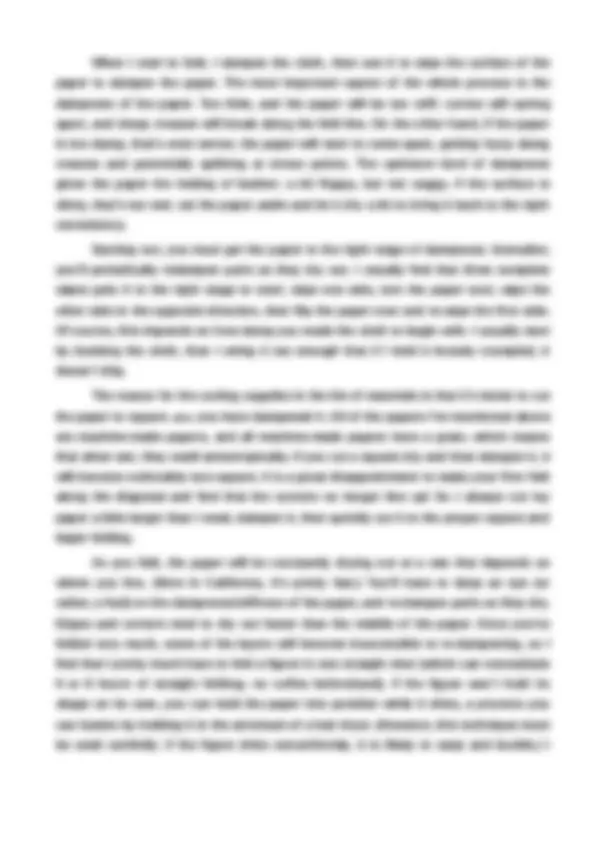
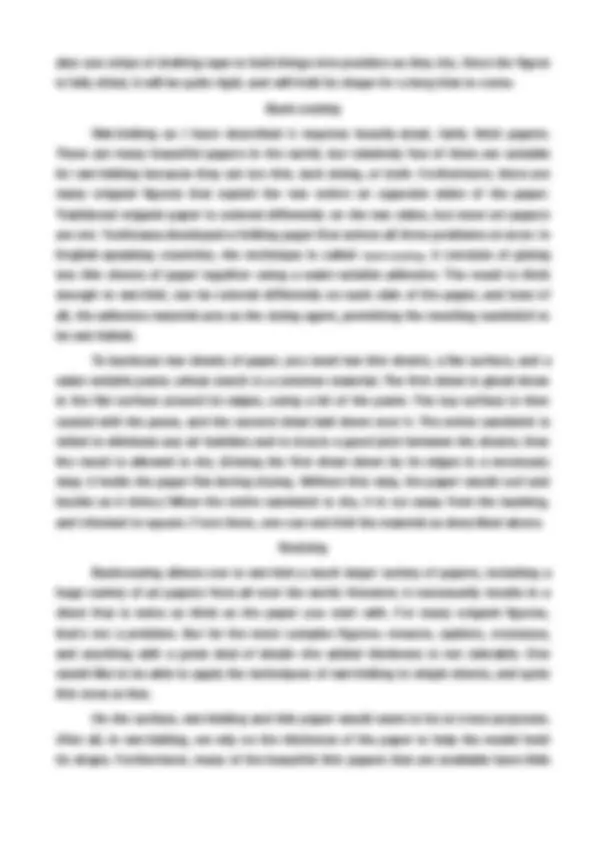
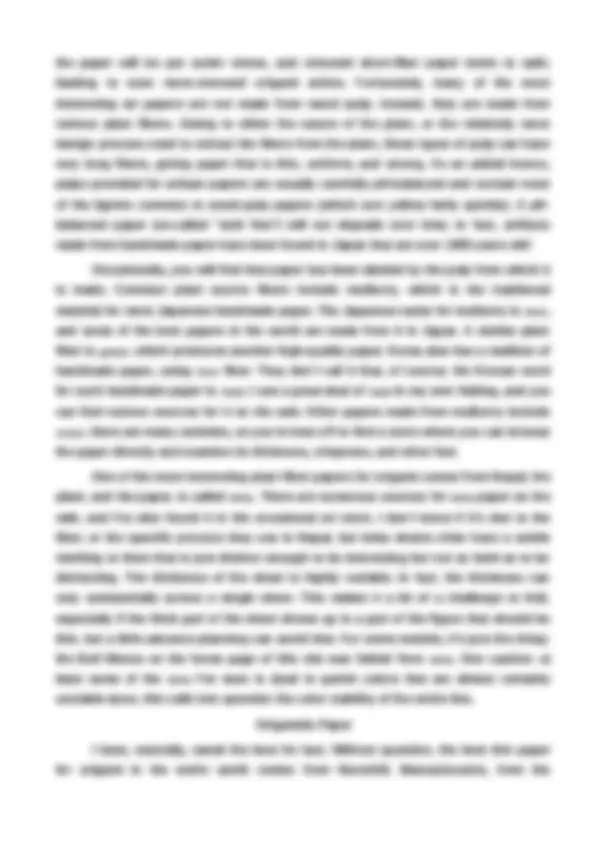
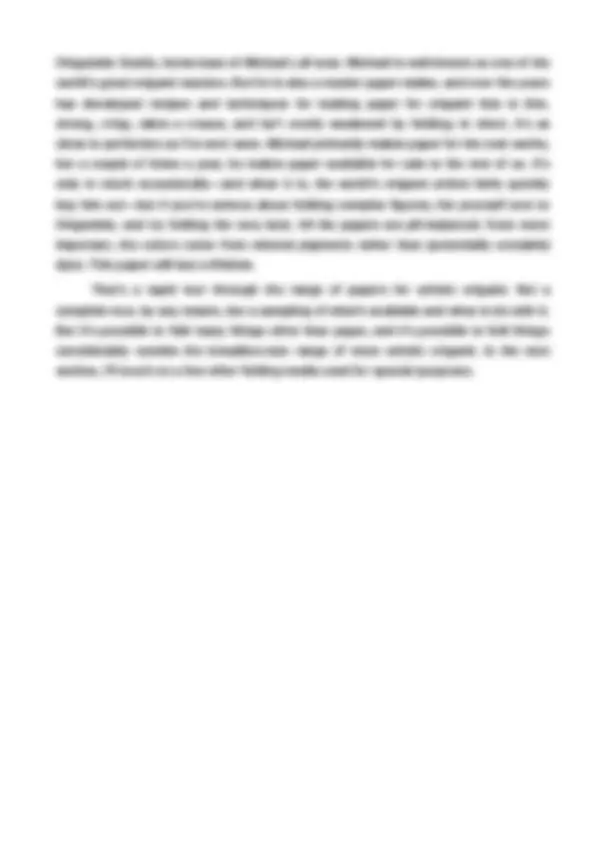
Estude fácil! Tem muito documento disponível na Docsity
Ganhe pontos ajudando outros esrudantes ou compre um plano Premium
Prepare-se para as provas
Estude fácil! Tem muito documento disponível na Docsity
Prepare-se para as provas com trabalhos de outros alunos como você, aqui na Docsity
Os melhores documentos à venda: Trabalhos de alunos formados
Prepare-se com as videoaulas e exercícios resolvidos criados a partir da grade da sua Universidade
Responda perguntas de provas passadas e avalie sua preparação.
Ganhe pontos para baixar
Ganhe pontos ajudando outros esrudantes ou compre um plano Premium
Comunidade
Peça ajuda à comunidade e tire suas dúvidas relacionadas ao estudo
Descubra as melhores universidades em seu país de acordo com os usuários da Docsity
Guias grátis
Baixe gratuitamente nossos guias de estudo, métodos para diminuir a ansiedade, dicas de TCC preparadas pelos professores da Docsity
Técnica de dobrar papel (origami), umedecendo o papel.
Tipologia: Notas de estudo
1 / 9
Esta página não é visível na pré-visualização
Não perca as partes importantes!
http://www.origami-resource-center.com/wet-folding-origami.html
Wet folding origami is a relatively new way of folding paper. It was developed by origami master Akira Yoshizawa and it involves moistening the paper before you fold it. The resulting model has a softer, textured look with gentle curving lines. Gilad’s web site shows the difference between a regular origami dog and a wet fold origami dog. Wow! [Puppy created by Francisco Javier Caboblanco; photo by Gilad Aharoni]
Wet folding origami is not difficult, but it does take practice. Here are some tips for success.
1. Practice folding the model the regular (dry) way before trying it wet. You need to be very familiar with the folding sequence because you will need to fold quickly when the paper is wet. 2. Use a spray bottle or a wet cloth to moisten the paper so that it is damp. The paper should not be dripping wet. Having the right amount of water is crucial – this will take a bit of trial and error. 3. Fold the model quickly with a sure hand. Press down with fingertips, not with fingernails. Avoid folding, unfolding, and refolding: this will cause the paper to tear or fray. 4. Allow the model to dry completely. Avoid handling and repositioning the model to make it better. Just let it dry. If the model unravels before it dries, use devices (such as elastic bands or clothespins) to preserve the model’s shape. 5. Repeat with different types of paper until you get the look you desire. In general, thick paper, such as elephant hide, works best. Robert Lang has a good article on Wet-Folding Papers.
http://www.langorigami.com/info/paper/wetfolding_papers.php
When the great Japanese master Akira Yoshizawa began visiting the West in the latter half of the twentieth century, his audiences were astounded at the organic, lifelike forms he had created. Much of the magic arose from his folding technique; rather than making every crease sharp, he incorporated soft creases, curved creases, and gentle, rounded forms. And yet, despite the softness of form, the folded figures themselves were often rigid, almost shell-like; they easily withstood the rigors of travel and retained their original form. The secret was a folding technique invented by Yoshizawa, called wet-folding. Nowadays the term "wet-folding" is used to refer to any of a family of techniques, and the original techniques developed by Yoshizawa have been expanded upon by many artists. The common element to all members of the family of wet-folding is the application of water to the paper to soften it during the folding process. This allows the formation of both soft and sharp creases and lets you easily form curved surfaces; then when the paper dries, it retains its shape, becoming rigid and resilient. With thin papers, wet-folding allows one to compress multi-layered flaps to a much finer degree than with dry folding, allowing a much more realistic expression for legs and antennae in arthropodic subjects. I took up wet-folding over 20 years ago, and over the years, have become enthralled by its capacity for variation and expression, to the point that nowadays, nearly everything I fold for display and most of the figures on this site are wet-folded.
There are now many different papers for wet-folding and many different styles of wet-folding. While you don't need to know a lot to wet-fold, if you're planning on exploring the technique, it is helpful to understand why it works, if only to understand why some papers work and other papers don't.
The thing that enables wet-folding is sizing. Sizing is a water-soluble adhesive that is—sometimes—added to the paper pulp during its manufacture. The sizing agent acts to bond the fibers of the paper together as the paper dries, resulting in a stronger, crisper sheet. Paper manufacturers use different types and amounts of sizing in their papers, depending on the properties they're after. For the origami folder, sizing is what makes wet-folding work. When you dampen the paper, the water dissolves the sizing, making the paper softer and more malleable; when the paper dries, the sizing bonds the paper fibers together in their
When I start to fold, I dampen the cloth, then use it to wipe the surface of the paper to dampen the paper. The most important aspect of the whole process is the dampness of the paper. Too little, and the paper will be too stiff; curves will spring apart, and sharp creases will break along the fold line. On the other hand, if the paper is too damp, that's even worse; the paper will start to come apart, getting fuzzy along creases and potentially splitting at stress points. The optimum level of dampness gives the paper the feeling of leather; a bit floppy, but not soggy. If the surface is shiny, that's too wet; set the paper aside and let it dry a bit to bring it back to the right consistency.
Starting out, you must get the paper to the right stage of dampness; thereafter, you'll periodically redampen parts as they dry out. I usually find that three complete wipes gets it to the right stage to start; wipe one side, turn the paper over, wipe the other side in the opposite direction, then flip the paper over and re-wipe the first side. Of course, this depends on how damp you made the cloth to begin with. I usually start by dunking the cloth, then I wring it out enough that if I hold it loosely crumpled, it doesn't drip.
The reason for the cutting supplies in the list of materials is that it's better to cut the paper to square after you have dampened it. All of the papers I've mentioned above are machine-made papers, and all machine-made papers have a grain, which means that when wet, they swell anisotropically. If you cut a square dry and then dampen it, it will become noticeably non-square. It is a great disappointment to make your first fold along the diagonal and find that the corners no longer line up! So I always cut my paper a little larger than I need, dampen it, then quickly cut it to the proper square and begin folding.
As you fold, the paper will be constantly drying out at a rate that depends on where you live. (Here in California, it's pretty fast.) You'll have to keep an eye (or rather, a feel) on the dampness/stiffness of the paper, and re-dampen parts as they dry. Edges and corners tend to dry out faster than the middle of the paper. Once you've folded very much, some of the layers will become inaccessible to re-dampening, so I find that I pretty much have to fold a figure in one straight shot (which can necessitate 6 or 8 hours of straight folding; no coffee beforehand). If the figure won't hold its shape on its own, you can hold the paper into position while it dries, a process you can hasten by holding it in the airstream of a hair dryer. (However, this technique must be used carefully; if the figure dries nonuniformly, it is likely to warp and buckle.) I
also use strips of drafting tape to hold things into position as they dry. Once the figure is fully dried, it will be quite rigid, and will hold its shape for a long time to come. Back-coating Wet-folding as I have described it requires heavily-sized, fairly thick papers. There are many beautiful papers in the world, but relatively few of them are suitable for wet-folding because they are too thin, lack sizing, or both. Furthermore, there are many origami figures that exploit the two colors on opposite sides of the paper. Traditional origami paper is colored differently on the two sides, but most art papers are not. Yoshizawa developed a folding paper that solves all three problems at once: in English-speaking countries, the technique is called back-coating. it consists of gluing two thin sheets of paper together using a water-soluble adhesive. The result is thick enough to wet-fold, can be colored differently on each side of the paper, and best of all, the adhesive material acts as the sizing agent, permitting the resulting sandwich to be wet-folded.
To backcoat two sheets of paper, you need two thin sheets, a flat surface, and a water-soluble paste; wheat starch is a common material. The first sheet is glued down to the flat surface around its edges, using a bit of the paste. The top surface is then coated with the paste, and the second sheet laid down over it. The entire sandwich is rolled to eliminate any air bubbles and to insure a good joint between the sheets; then the result is allowed to dry. (Gluing the first sheet down by its edges is a necessary step; it holds the paper flat during drying. Without this step, the paper would curl and buckle as it dries.) When the entire sandwich is dry, it is cut away from the backing, and trimmed to square. From there, one can wet-fold the material as described above.
Resizing Backcoating allows one to wet-fold a much larger variety of papers, including a huge variety of art papers from all over the world. However, it necessarily results in a sheet that is twice as thick as the paper you start with. For many origami figures, that's not a problem. But for the most complex figures—insects, spiders, crustacea, and anything with a great deal of detail—the added thickness is not tolerable. One would like to be able to apply the techniques of wet-folding to single sheets, and quite thin ones at that.
On the surface, wet-folding and thin paper would seem to be at cross purposes. After all, in wet-folding, we rely on the thickness of the paper to help the model hold its shape. Furthermore, many of the beautiful thin papers that are available have little
results are well-worth the effort; most of the insects on this site were folded using this technique. Instead of using plain water, you can also dissolve some MC in the water used for dampening; this will add additional strength to thin features after it has soaked in and dried.
Sizing Agents Methylcellulose is probably the most common sizing agent used in wet-folding, but there are several others. Less easily obtained is Sodium Carboxymethylcellulose, a.k.a. CMC. Chemically, CMC is more polar than MC, which makes it bind more tightly to the cellulose fibers of the paper. In layman's terms, the paper is stiffer when it dries. Even stronger than MC and CMC are the various starch-based adhesives, with wheat starch being the most common. All three are used in book conservation and have a good record of longevity. However, starch-based adhesives are attractive to vermin; no origami will survive being chewed to death by insects. Wheat flour is about 10% protein, which makes it particularly attractive to our multi-legged friends; MC and CMC are relatively inert (and I only use them in my own work). In any case, a few mothballs tipped into the storage box will keep the nasties away.
Thin Papers Now that you know what to do with them: what thin papers should you use? There is an enormous variety of wonderful thin papers from around the world—far too many for me to discuss. But I will mention here a few of my favorites.
Many of the good thin papers for folding are handmade, and most of them are made from plant fibers other than wood pulp. In general, you should avoid papers made from wood pulp (which takes in the vast majority of the paper made in the world). Wood pulp for paper is made by grinding up wood chips by one of two processes. Thermo-mechanical processing (TMP) primarily uses heat, steam, and grinding to break the chips down into individual fibers; chemical pulp uses acid and other harsh chemistry to break down the cellulose and lignins (and incidentally, gives paper mills their distinctive, and long-ranging, smell). TMP must grind the chips into small bits for the steam to do its work, and so, despite its (relative) environmental friendliness, the paper fibers are shorter and weaker than those in chemical pulp. Most commercial paper is made of a blend of the two, with lower grades (like newsprint) having a higher proportion of the short-fibered TMP pulp.
Short fibers are bad for folding, and they are really bad for thin papers for folding. Thin papers usually mean complex figures, and complex figures usually mean
the paper will be put under stress, and stressed short-fiber paper tends to split, leading to even more-stressed origami artists. Fortunately, many of the most interesting art papers are not made from wood pulp; instead, they are made from various plant fibers. Owing to either the nature of the plant, or the relatively more benign process used to extract the fibers from the plant, these types of pulp can have very long fibers, giving paper that is thin, uniform, and strong. As an added bonus, pulps provided for artisan papers are usually carefully pH-balanced and contain none of the lignins common in wood-pulp papers (which turn yellow fairly quickly). A pH- balanced paper (so-called "acid free") will not degrade over time; in fact, artifacts made from handmade paper have been found in Japan that are over 1000 years old! Occasionally, you will find that paper has been labeled by the pulp from which it is made. Common plant source fibers include mulberry, which is the traditional material for most Japanese handmade paper. The Japanese name for mulberry is kozo , and some of the best papers in the world are made from it in Japan. A similar plant fiber is gampi , which produces another high-quality paper. Korea also has a tradition of handmade paper, using kozo fiber. They don't call it that, of course; the Korean word for such handmade paper is hanji ; I use a great deal of hanji in my own folding, and you can find various sources for it on the web. Other papers made from mulberry include unryu ; there are many varieties, so you're best off to find a store where you can browse the paper directly and examine its thickness, crispness, and other feel. One of the most interesting plant fiber papers for origami comes from Nepal; the plant, and the paper, is called lokta. There are numerous sources for lokta paper on the web, and I've also found it in the occasional art store. I don't know if it's due to the fiber, or the specific process they use in Nepal, but lokta sheets often have a subtle mottling to them that is just distinct enough to be interesting but not so bold as to be distracting. The thickness of the sheet is highly variable. In fact, the thickness can vary substantially across a single sheet. This makes it a bit of a challenge to fold, especially if the thick part of the sheet shows up in a part of the figure that should be thin, but a little advance planning can avoid that. For some models, it's just the thing: the Bull Moose on the home page of this site was folded from lokta. One caution: at least some of the lokta I've seen is dyed in garish colors that are almost certainly unstable dyes; this calls into question the color stability of the entire line. Origamido Paper I have, naturally, saved the best for last. Without question, the best thin paper for origami in the entire world comes from Haverhill, Massachusetts, from the